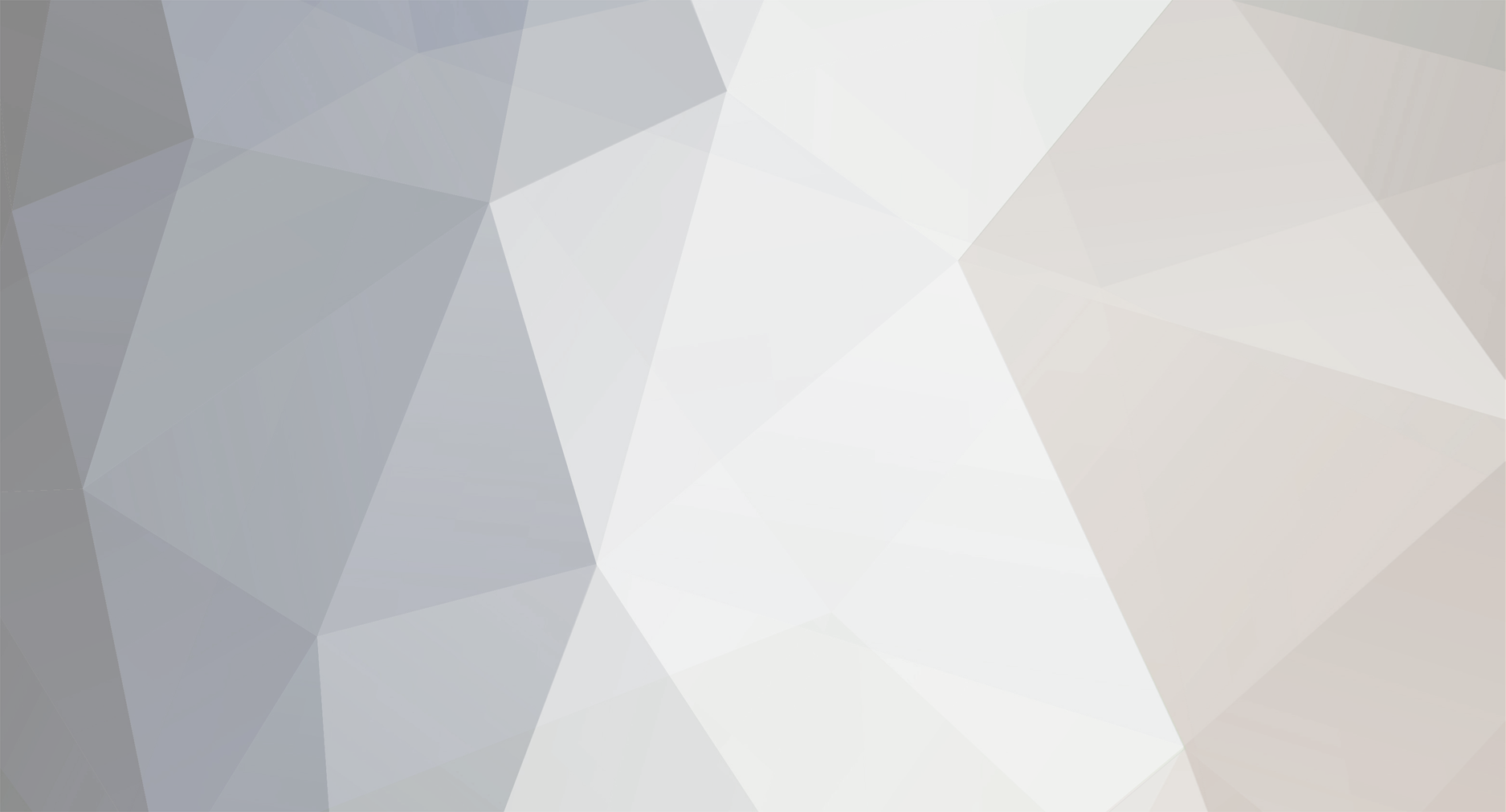
Kevin McAllister
Member-
Posts
5,172 -
Joined
-
Last visited
Reputation
1,596 SpectacularPersonal Information
-
Location
Vancouver, Canada
Recent Profile Visitors
The recent visitors block is disabled and is not being shown to other users.
-
Closing nurbs surface into a solid
Kevin McAllister replied to Kevin Huynh's topic in General Discussion
If all that's required is some holes in the NURBS surface, the Project tool is the right tool for the job. Kevin -
Is anyone else having issues with Callout text sizes randomly changing in Annotations on Sheet Layers? It usually scales to some huge font size, taking over the page. At first I thought it was only callouts brought forward from older versions but now it seems to randomly happen to any callout. Kevin
-
Objects View plans on viewports - Hybrid Objects
Kevin McAllister replied to Cristiano Alves's topic in General Discussion
Are you able to share the file from your example? Mark Doubleday's video on schematic views may be helpful to you - Kevin -
Objects View plans on viewports - Hybrid Objects
Kevin McAllister replied to Cristiano Alves's topic in General Discussion
It looks like part of your object (a symbol within a symbol) was not designed to be rotated in 3d. The plan view of one of the elements is out of sync with its 3d view. Note that all of the various 2d views within a symbol are user generated. If it's a stage lighting setup there are specific methods to present instruments hung on booms. Kevin -
Updating from Mac OS 14.4.1 to Mac OS 14.5 solved the issue. Kevin
-
Rectangle to Walls - always one unjoined corner
Kevin McAllister replied to Benson Shaw's question in Troubleshooting
Solved here too. The tool problem and the wall problem. Updating my Mac to 14.5 solved my tool problem. Update 5 seems to solve the wall issue. Kevin -
Hello, I just got notified and updated to Vectorworks 2024 Update 5. When I started up Vectorworks after the update none of the tools from the tool palettes work. I can select them, but they won't draw, navigate or work in the drawing (both new and existing). The menu commands work fine as do the contextual menus. Its like the tools system is down. What's the recommended troubleshooting for this? I've done a restart etc.. Do I need to do a reinstall? Are others having this issue? Kevin
-
Rectangle to Walls - always one unjoined corner
Kevin McAllister replied to Benson Shaw's question in Troubleshooting
I get the same result here - an unjoined corner. It's the same corner that would be open if you converted the rectangle to a NURBS curve. Noting that Benson's signature says Update 4 and Tom's says Update 5. I'm using Update 4.1. Kevin Edit> I updated to Update 5 to test this and now none of my tools work, sigh 😔