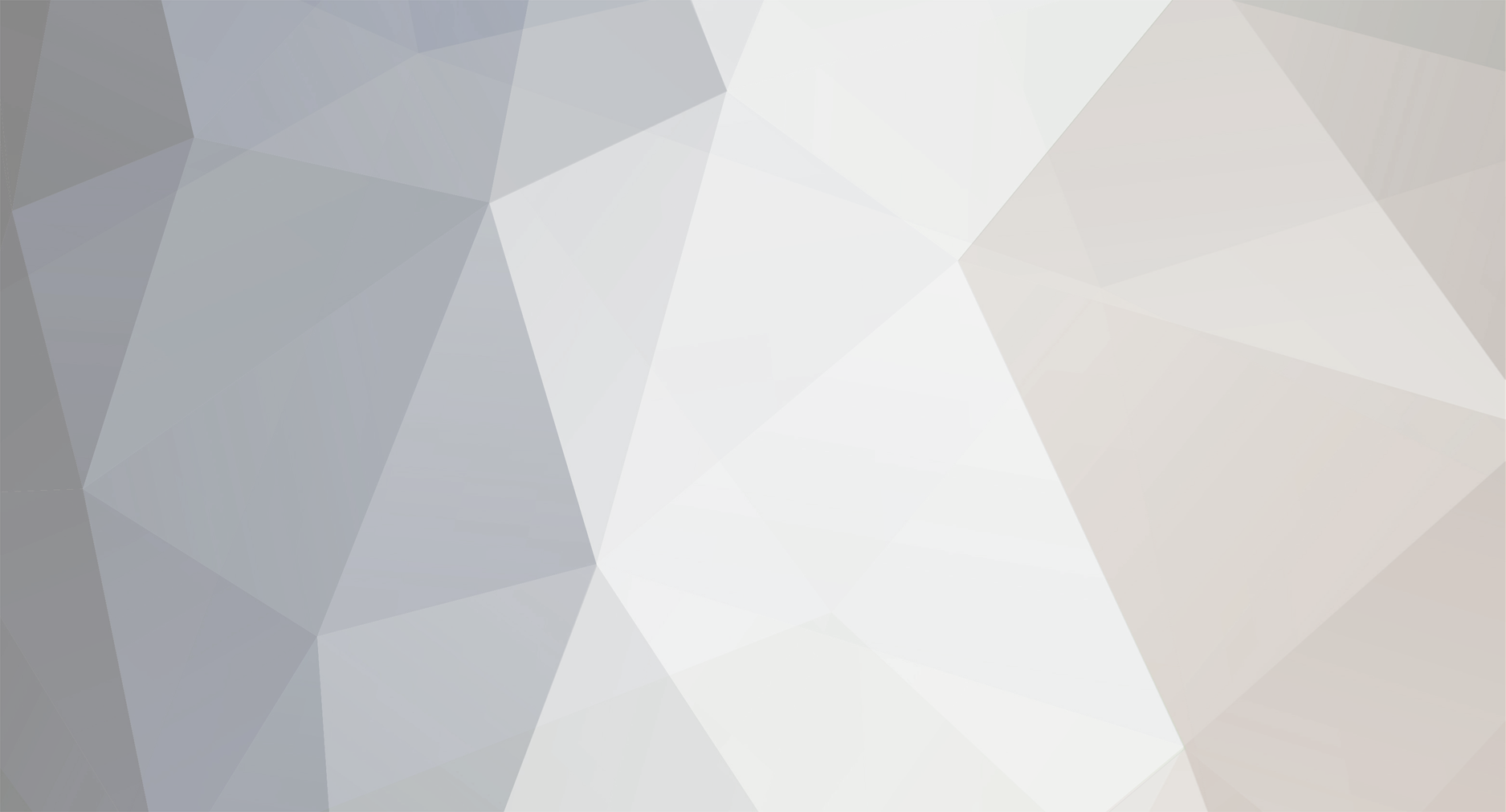
Benson Shaw
Member-
Posts
4,316 -
Joined
-
Last visited
Reputation
1,302 SpectacularPersonal Information
-
Occupation
Public Artist
-
Homepage
www.bensonshaw.com
-
Location
United States
Recent Profile Visitors
The recent visitors block is disabled and is not being shown to other users.
-
Also - If hardscape 3d display curvature is is changed via the simplification tolerance, a double click of the Hardscape launches the Reshape tool and reveals vertices of the Path (no need to right click>edit path) for edit - not converted to some polygon with many facets. Edits can be made in 3d views as if editing that simple 2d polyline. Changing the Simplification Tolerance in the OIP does not affect the vertex count near bottom of the OIP. eg in my example above, the vertex count is 8 in each iteration of the simplification value. -B
-
In my tests - Adjustments to the 3d simplification tolerance, eg in Hardscape OIP, do not affect the source object geometry. Those original Arcs, Bezier and spline curves in the source polyline are present for edit via right click Edit Path pane. TopPlan always displays the curves as the source obj . Perhaps others can comment on performance and print/save issues of complex files with super low tolerance settings for such DTMs and site mods? I don't have any big, complex files to compare. -B
-
Ahhh! That's it!! @Tom W. - brilliant, as usual. For this Hardscape, the value defaulted to .083. Tried value of 1, which essentially eliminated all the curves and subbed in a single point. And decreasing values. .001 did the trick. The Edit Path window shows the orig source with the beziers intact. -B
-
Hardscapes, and some other vwx objects, display faceted edges from smooth 2d source curves, eg bezier and spline. In the case of Hardscapes, Top Plan view does not show facets. But 3d views show a facet at each curve vertex. A workaround is to convert the source polyline (with curves) to a polygon. No curves, but probably lots of vertices which can slow down redraws and renders. Vertex count in this revised source can be reduced via Modify>Drafting Aids>Simplify Polys. Workaround is only a few steps, and helps the display at close zoom. But new edge is difficult to edit. Often easier to draw a new source polyline with bezier or spline points with subsequent and conversion and simplify. Big effort if lots of changes to several edges over design life. So save the original source poly! It might come in handy. Anyone have a better process? Example starts with 8 vertices. Convert to polygon produces 1027 vertices. Simplify Poly takes it down to 31. Facets nearly invisible at 31. But edits probalby best as do over. -B PS - this is not a 2d/3d conversion pref issue or render quality setting (both Very High), or layer raster resolution (300). Hardscape facets.vwx
-
This is a new mode for the selection tool, added in v2024. Change the mode in the Mode Bar of your Vwx interface - the modes are in the upper left corner of your screen. Choose instead one of the other modes by clicking one of the other 3 icons. I will get back to keyboard and offer an image, if others do not post before. -B
-
Zoom 3D screen image wrong after rotation
Benson Shaw replied to WhoCanDo's question in Troubleshooting
Zoom effect does not happen on my vwx2024 installation or MacOS system. I tested duplicate/drag/rotate CW/zoom in several views (front, top, iso) and several rotation via shortcut, Rotate tool, and Rotate 3d. Zoom via mouse wheel and shortcuts. Acts as expected. Sorry, no clue about your experience. -B -
Zoom 3D screen image wrong after rotation
Benson Shaw replied to WhoCanDo's question in Troubleshooting
Could this be a Far From Origin issue? The cursor x,y locator at lower right of your screen is hard for me to read, but seems to be in range of -21000,10000. or? If drawing units are feet, or meters, then that’s Far enough to cause problems. If units are mm, then not the issue. just an idea -B -
I’m becoming more frequently aware of “missing” features and capabilities in older tools and processes. This DAP is a likely example. Possibly unchanged since mcd? Users and developers realized that an option to preserve the source objects enhances the vwx experience, and the option was built in to new tools. The oft expressed desire to have tool and command updates is understandable. I often share it. I don’t know reasons for lack of such modernization, but I can think of a few possibilities, not all of them cynical: Update might break objects when porting between older and newer versions. Eg some rotation functions use positive values in clockwise direction, others in anti clockwise. Making all consistent could change rotation dependent objects when porting. Update time and expense conflicts with development of perceived or real need for new stuff. This involves long term planning, marketing, keeping up with competing products, etc. Old tools functions replaced by newer tools and strategies. Eg screen plane Specific workarounds are easy enough to discover and implement. Therefore complaints are limited. Eg the DAP - get in habit of duplicating source objects. Incremental improvements to newer functions take precedence. Eg slab, to aligned slab, to draped slab, concurrent with introduction of landscape area with components. . . lots more i can’t imagine I’m overall very happy with the constant improvements we do receive. But stand by for all my future gripes. -B
-
Creating a viewport from design layers
Benson Shaw replied to Monique Freese's topic in Architecture
@Monique Freese The Alert notice might be missing because during a previous VP creation, you checked the "Always do the selected action" option. In this case, it would mean that the Alert would not appear. Instead, the Create VP dialog would appear. After closing the Create dialog, the VP will appear on the sheet as directed by the VP Create dialog. If this is the cause, and, for some reason, you want the Alert to appear, you need to reset the Vectorworks pref>Sessions>Reset saved settings. Note that this resets for ALL types of Always do warnings. No current way see a list and pick relevant items. -B -
Creating a curved wall or extrude from a 2d elevation
Benson Shaw replied to Jim Dougherty's topic in Site Design
Try the Deform tool in Bend mode: Draw your skyline, eg on the layer plane. Then work on a duplicate of the skyline. Change the view away from Top, eg via flyover, or use iso. Select the duplicate . . . Rotate 3d 90° to stand it up on the x axis. (it's still a 2d object) Extrude it. Use negative value (extrudes away from view), or can be 0. Engage the Deform tool, set to Bend Solid > Symmetric mode Control bend amount visually, with guide objects on layer plane, or numeric by pressing tab for cursor fields. Make sure the protractor is on the layer plane. Some advantage to 0 extrusion for planning construction. Vertical frame posts and studs can be inserted, and will not have curved faces. -B Skyline bend(1).mov -
@mjsmithvt also check out these threads/posts regarding walls with slanted, canted, or otherwise shaped profiles, via insertion of a wall cut symbol: and -B
-
@Stephan Moenninghoff Brilliant! This two step process eluded me. Not sure I would have ever discovered that separate deforms on different planes is the answer. Many thanks for revealing. I tried on a couple generic solids made from extrusions of my 2d sample. One worked. Deform failed on the other. Some persistence may be required. -B
-
@Brandon Kleiman @Jeff Prince has it correctly re skewing 3d models similar to video in your link. Buuuht . . You might be able to get close with the shear tool. Only works on 2d objects, or groups of them. So, no PIOs for walls, windows, etc. End result is polylines, or group thereof, which can be extruded or otherwise modified. For scenery, perhaps this is enough for layout and fab work? -B Shear(1).mov
-
Artifact in a viewport, looks like a shadow, but from what?
Benson Shaw replied to unearthed's question in Troubleshooting
Thoughts To me, this looks like an artifact eg from a dwg/dxf imported or converted file. Especially an arc with associated fill back to its center. Object might have custom attributes rather than “by class”. I cannot explain the rounded corners. It might be a stray nested in a hybrid symbol (part of a former dwg block?), or in a group? The symbol/group extent is much larger than the shadow thing, so cannot be selected with marquee around the shadow. Try Select All and zoom to selection. Might be worth an old fashioned search via class shutoffs. Make a duplicate test file with a saved view to return to current state, then turn off half of the classes. If still visible, turn on that half and turn off the other half. If gone, turn on half of those, etc until the object’s class is isolated and the object can be found, selected, and interpreted. -B