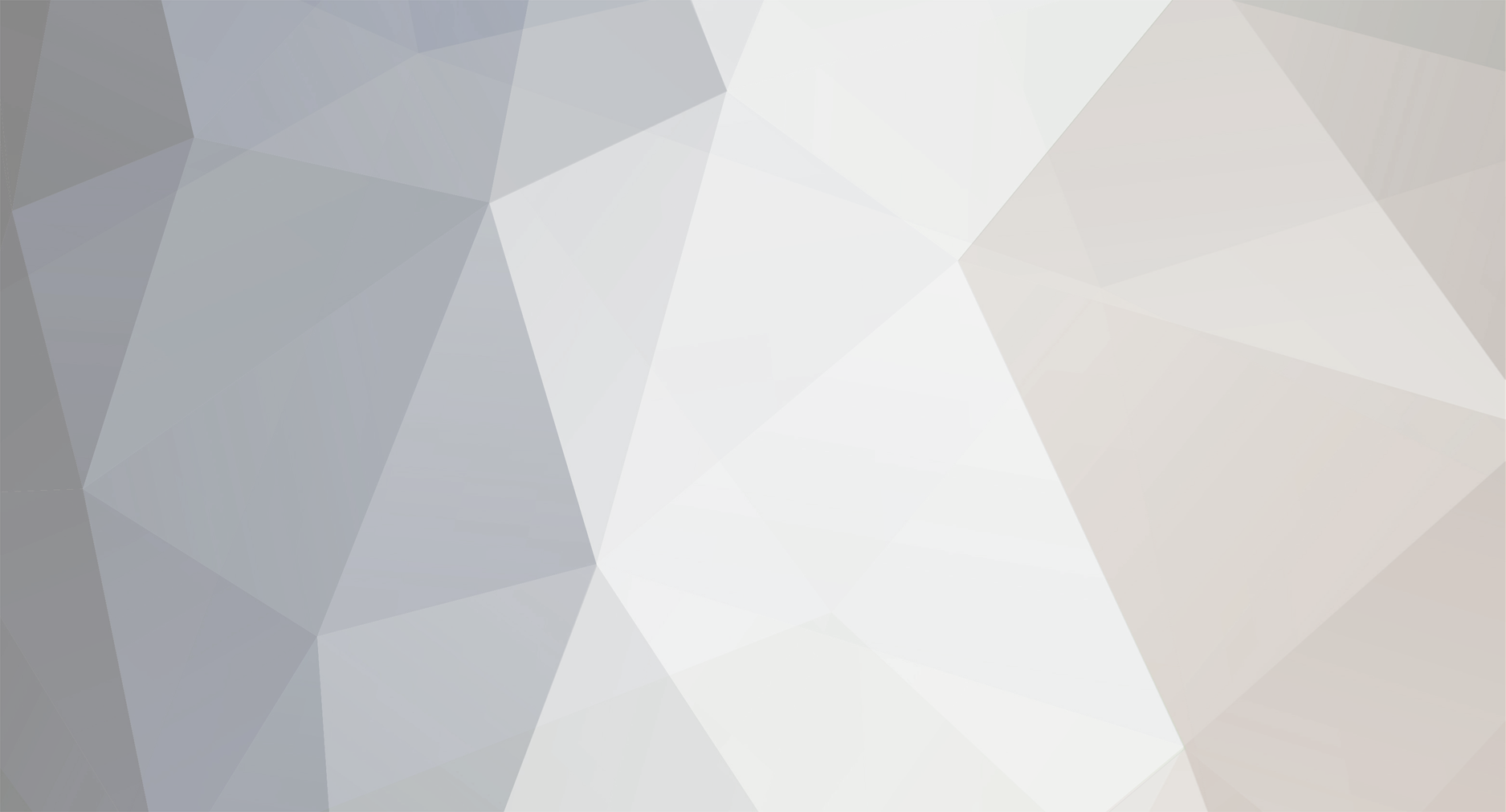
Kevin McAllister
Member-
Posts
5,191 -
Joined
-
Last visited
Content Type
Profiles
Forums
Events
Articles
Marionette
Store
Everything posted by Kevin McAllister
-
Hello, I've been a Vectorworks user since 1994 (Minicad 5). I mainly use it for theatre and is often the case in the industry I am single person design business. My comments are about Vectorworks marketing. One of the most important things in marketing is know your audience. When I bought my Vectorworks license through Paxar Technologies they knew exactly who I was. When Vectorworks took over and opened a Vancouver office I became an email address. Vectorworks often sends marketing "deals". I don't think I've ever qualified for any of them (always deals on new licenses). I just feel spammed and wonder why am I receiving this offer. Here's the current example - And here's the fine print - I will only ever need one license and its current. I can never be a new customer (user since Minicad 5). I use service select so this info should be on file. I guess I stay on the mailing list thinking that one day I'll get a deal for being a loyal (30 years and counting) user..... 🙃 It really seems a waste to use these marketing dollars on me...... and I'm sure I'm not alone thinking this. Kevin
-
Stage Deck Tool - Xs
Kevin McAllister replied to Andy Broomell's question in Wishlist - Feature and Content Requests
I'll second that bump. KM -
I thought that might be the case 😔 @JuanP is correcting this on the roadmap somewhere? Thanks, Kevin
-
I've been having this same issue, both in Vectorworks 2024 and now in Vectorworks 2025. I've tried a variety of things to combat the shift, including making sure all my images for textures are converted to CMYK before importing them into Vectorworks, but the colour shift still happens. Quality of colour output is important in design. Its difficult when the intended colours don't transfer to output shared with clients. How do we solve this? Kevin Screen shot from Vectorworks vs. Screen shot of PDF output. The colours are more garish and saturated.
-
Just to confirm, since it's not clear from the screen shots, you need to select Custom from the dropdown in the 3D Options dialog to change the "texture" of a Softgoods object.... I have seen other anomalies myself but this wasn't mentioned above. Closing and reopening a file can sometimes help, but a full restart is a sure way to differentiate between an anomaly and a corrupt object or bug. Kevin
-
Lock Proportions
Kevin McAllister replied to Kevin McAllister's question in Wishlist - Feature and Content Requests
Yay! This was implemented in Vectorworks 2025! See screen shot. Amazing that this wish is almost 15 years old! Kevin -
Ah ha! There's the distinction. Closing the window vs. quitting the application. I've always been quitting it to remove it from the dock. Why not build the status dialog into the menu bar icon rather than having to open a window? Each time I use Cloud Services I need to remind myself how the interfaces work. It's a bit convoluted. Kevin
-
Objects View plans on viewports - Hybrid Objects
Kevin McAllister replied to Cristiano Alves's topic in General Discussion
This is the bug thread I was referring to - @Cristiano Alves what version of Vectorworks are you running? Your signature shows 2023.... KM -
Objects View plans on viewports - Hybrid Objects
Kevin McAllister replied to Cristiano Alves's topic in General Discussion
I'm pretty sure this must be a bug of some sort. Somehow the 2d and 3d parts of the lighting position are out of sync. Usually these are managed in a symbol but these positions aren't connected to a symbol, at least not one that users can see. There was a symbol creation bug not too long ago where the 2d component used the document origin for its origin but the 3d component did not. I wonder if it's affecting this plugin. Kevin -
Ha I just used the same example and then saw your reply..... KM
-
So you're still switching to the Flyover tool and then back to another tool? Just using single key keyboard shortcuts. My comment is about wanting a boomerang style switch to the Flyover tool without using a middle mouse button, so you can rotate the view without disturbing the current tool mode. Your method doesn't allow for maintaining selections within tools - eg. rotating to select additional edges when using the 3d fillet tool. KM
-
Partly true. The hotkey requires a middle mouse button along with the hotkey to invoke flyover. All Macs and most laptops don't come off the shelf with a middle mouse button. Kevin
-
Not entirely true. There's no easy way to quickly switch to orbit (Flyover tool) without a three button mouse. Navigation should be independent of tools, period, just like every other 3d program out there. Even the free slicing software for 3d printing has better navigation than Vectorworks, a professional level piece of CAD software at a premium price. Kevin
-
Looks useful 😊. I guess it's a step towards making navigation inherently part of the interface instead of tool based which is my longstanding wish. Kevin
-
Hello, I would love the ability to show only 2d, only 3d or hybrid symbols when searching in the Resource Browser. I hardly ever use 2d only symbols and sometimes the search results in the Resource Browser can take a fair amount of time to wade through. Being able to filter by symbol type would be useful. Kevin
- 1 reply
-
- 5
-
-
Polyline Reshape Tool BUG- Tool Modes wrong icons
Kevin McAllister replied to Bill_Rios's topic in General Discussion
What version of Vectorworks are you running and what operating system? It seems ok on Vectorworks 2024 Update 6 on a Mac..... Kevin -
Closing nurbs surface into a solid
Kevin McAllister replied to Kevin Huynh's topic in General Discussion
If all that's required is some holes in the NURBS surface, the Project tool is the right tool for the job. Kevin -
Is anyone else having issues with Callout text sizes randomly changing in Annotations on Sheet Layers? It usually scales to some huge font size, taking over the page. At first I thought it was only callouts brought forward from older versions but now it seems to randomly happen to any callout. Kevin