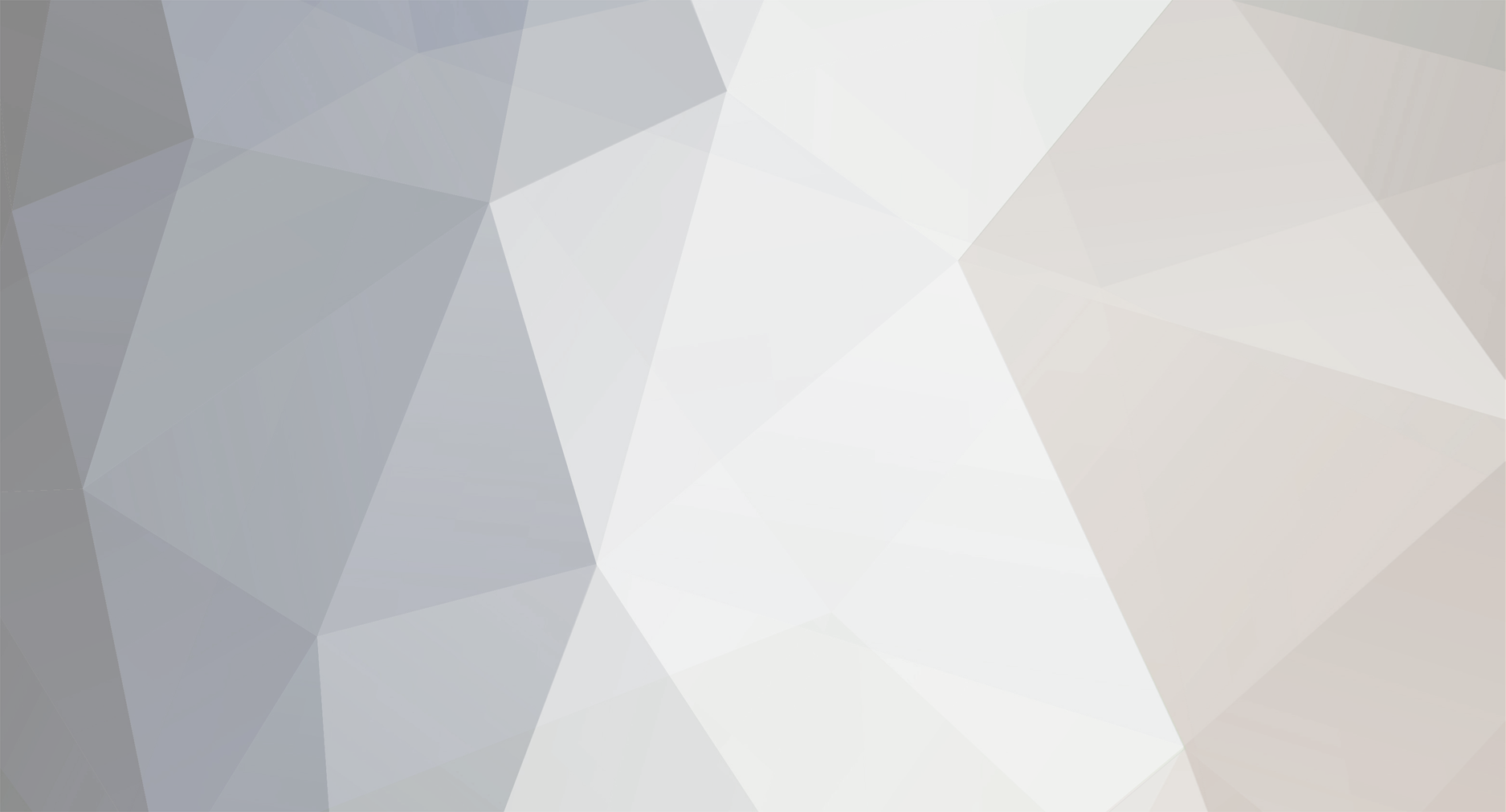
jcogdell
Vectorworks, Inc Employee-
Posts
960 -
Joined
-
Last visited
Content Type
Profiles
Forums
Events
Articles
Marionette
Store
Everything posted by jcogdell
-
The problem is that Spotlight doesn't use the channel number as the internal identifier since it can change based on design and user requirements, which would then break any connection (internal to Spotlight or external) to the any other linked data. You can try using the worksheet criteria ='Lighting Device'.'UID' to access the UUID's and this may enable you to correctly map the data. What software are you using to create the patch? If it supports MVR this may provide another route to get the data in and sync it to the correct lights.
-
To remove the hanging bracket you will need to edit the symbol definition. first thing you need to do is import the bumper into your active file, either by inserting one on a design layer or by right clicking on it in the resource manager and selecting import. Next you need to edit the 2D and 3D components of the smybol. to this right click on the bumper symbol in youractive file resources and select either edit 2D component or 3D component. This will enable you to edit the symbol definition. Once you have completed your edits rename the bumper and save the file into either a user or workgroup library folder so its available for future projects
-
The issue here is how to ensure that the correct data in the excel sheet is linked to the correct lighting device. We do support exporting and importing csv files with lighting data but this relies on using the hidden unique identifier (uid) for each lighting device instance in the design. Without this Spotlight doesn't know which lighting device is which. In practice this means that the original csv data has to be created in Spotlight so that the correct uid data is included. Where is the patch data coming from? There maybe a possible workaround or solution available.
-
Fill in the position name field for the truss sections in each tower (group select and give all the truss sections in each tower the same name) Set your report criteria to 'type' 'is' 'truss' and then use 'field value' 'position name' 'is' and then enter the name of the tower in the last column. In the coulmns section use records Truss Position Name Truss Name and then function =Count This will give a report listing the type of truss sections used in the tower and a count for each along with the position name. Repeat this for each tower and apend the worksheets to the first one.
-
Can't find the event design tab in VW 2024
jcogdell replied to Garfield2039's question in Troubleshooting
The Spotlight workspace and menu structure was reorganised in the 2024 release, so that tools, features and commands are grouped by department/discipline. You'll find the event design commands in the event sub menu of the Spotlight menu. -
Single Face Texture Tool still does not work
jcogdell replied to MGuilfoile's question in Troubleshooting
@MGuilfoile Have you contacted Tech support about this issue? It sounds like something that is deeper than a simple fix and they can have one of our developers take look to find out what is going on. -
MVR export : focus information
jcogdell replied to Light-House's topic in Vision and Previsualization
What focus data are you trying to export with MVR? The MVR only includes a limited amount of focus data. Currently this is pan, tilt, shutter cuts and zoom. -
This is s known issue and the dev team is working to fix it. At the moment the only workaround I have figured out is to drastically increase the size of the text (300 or 400pt+).
-
Single Face Texture Tool still does not work
jcogdell replied to MGuilfoile's question in Troubleshooting
@MGuilfoile Have you tried using the 'Reset All Plugins' command from Tools>Utilities menu? This should address this issue. Another option is to use the 'Batch Convert' command from the file menu, though this is normally fro converting all your library files in one go. Both of these commands are designed to update objects and symbols in user files when a new version of Vectorworks is released. -
@StephenHuman Sorry, the only option would be to duplicate the original tower and lights, once you are happy with its configuration, and place the duplicates into the correct locations. MVR like Spotlight relies on the lights and other objects being unique otherwise there is no way to associate the patch data (or any other data) with an individual light.
-
My bad @spettitt is correct the plugin doesn't support extrude along path object yet. For simple geometry converting generic solids is the way to go, however for more complex geometry its better to convert to 3D polys before exporting as SoundVision will have better performance. I'll reach out to L-Acoustics and ask about this
-
@Dan stewart In the simplification dialogue you need to change the other symbols drop down, in your image it is set as do not export. Although not an issue in your example above, another issue to be aware of, is that the plugin doesn't support subdivision objects, these should be converted into 3D polys before exporting.
-
Hi Alex You need to download the library file onto your computer before yopu can edit it. You can do this by right clicking on the library and choosing download in the context menu.
-
Yep thats the settings, The top group (the Default Bridle Parameters) in the bridle preferences define the primary insertion parameter. Only one of the defaults can be active at a time and any bridle or deadhang drop that you insert has to meet the parameter criteria, such as the brilde apex is at 5m or the downleg must be 1m, otherwise you won't be able to draw the bridle or drop. When using the insert connection tool or insert drops command try to use either the down leg or leg length parameters as the primary insertion parameter and set it to a very short length (say that of a shackle). This should then make it easier to use and ensure that the deadhang gives a realistic result.
-
From the error message you likely need to adjust your default insertion setting in the Bridle settings dialogue. The apex is propably set or set too high for the trusses you are trying to connect
-
From the second image it looks like the straight truss and the corner are not properly aligned but without seeing the file I can't say for certain if its a drawing error or a probelm witht he truss librayry used. Can you post a file with the problem truss system in it, so I can take a look?
-
Another option is to use the replace lighting device button in the Lighting Device OIP to link the imported default to a Spotlight symbol Group select all the lights of the same type, and hit the command.
-
We're looking at a potential solution but I don't have a definite schedule yet.
-
Yes the main difference is you need to define the hanging bar as a T-corner in the Truss properties dialogue (accessed from the right click context menu) and then add the magnet locations using the XYZ fields.
-
Creating new cable parts in cable configuration
jcogdell replied to Sam Jones's topic in Entertainment
This has already been fixed, I think since update 2 2024, but it was definetly working last time I checked it. -
@Iainy1961 Have you tried the DMX patch interface? It works in a similar fashion to console patch interfaces, the key thing is to make sure all your fixtures have the channel ID's assigned so you can easily identify them. Patching this way will automatically make sure that the addresses fall inside the universe ranges, with any fixtures that end up out of the universe range automatically moving tot he next universe. It also displays how full the universes are visually and fixtures can be moved around graphically in the patch just like a console
-
Vectorworks 2024 not running after update
jcogdell replied to thomasone's question in Troubleshooting
@PNWPaul Its possible that your resource manager cache has gotten corrupted, navigate to your user folder, should be somthing along the lines of C:>Users>yourname>Appdata>Roaming>Nemetschek And look for a folder named Vectorworks RM cache either delete it or rename it and restart Vectorworks. This forces Vectorworks to re index the library and create a new cache. If this doesn't fix the issue please contact your local tech support -
To expand on @Scott C. Parker solution you could also set the hanging bar up as a T-corner, this would add a third magnet into the symbol and remove the need to edit the other library files to work correctly witht he hanging bar
-
Create Calculation Report does not retain Project Information
jcogdell replied to Projx_CA's topic in Braceworks
Hi @Thomas K. Its fixed in update 4, so available fairly soon -
@Charlie Winter I know this isn't necessarilly helpful for the current show you're working on but have you tried asking the MA team if they can add some tools/features to the MA3 patch interface to help with this? In my experience they listen to their users and are always on the look out for way to improve their software.