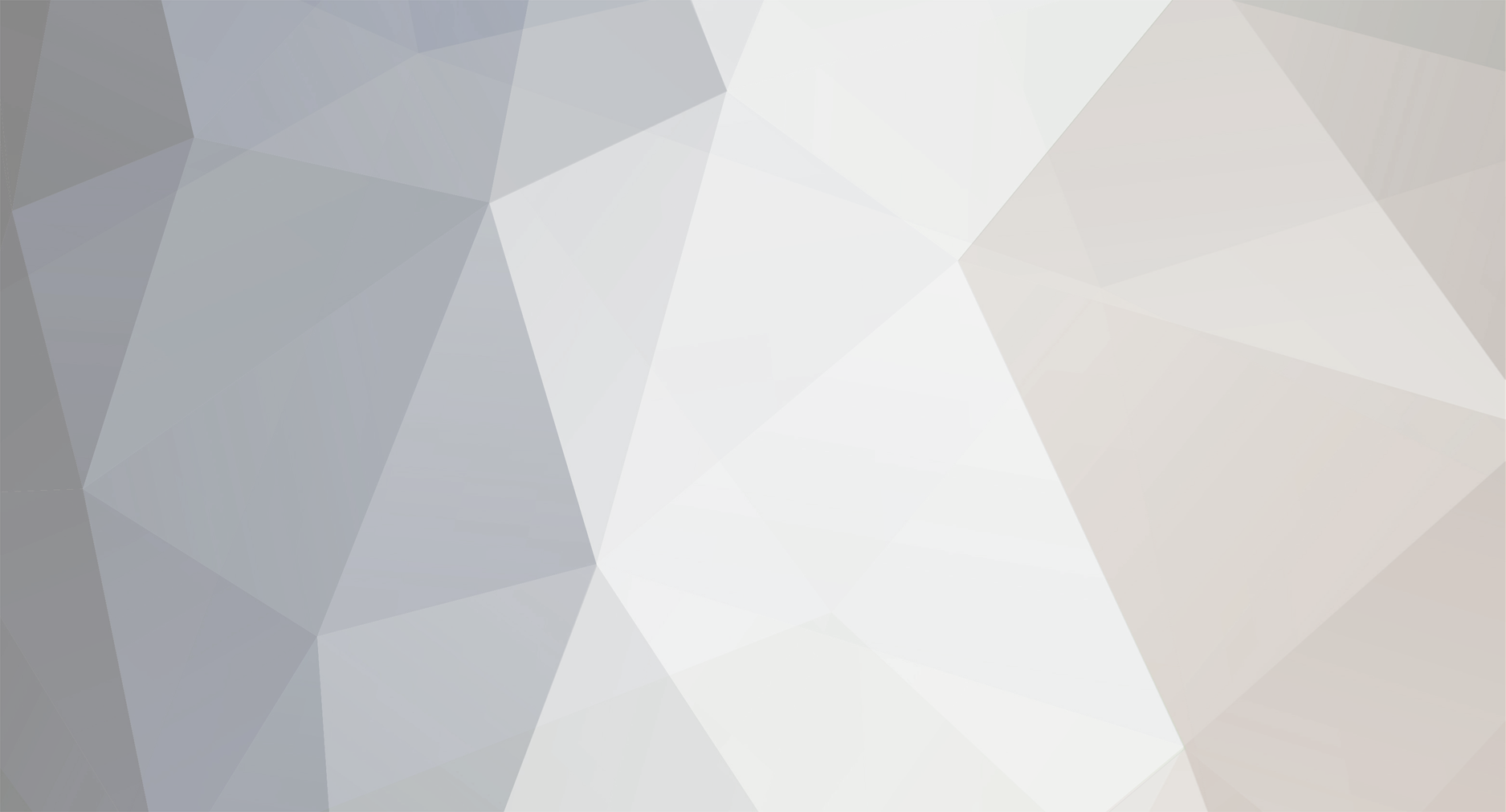
jcogdell
Vectorworks, Inc Employee-
Posts
1,049 -
Joined
-
Last visited
Reputation
428 SpectacularPersonal Information
-
Location
Germany
Recent Profile Visitors
The recent visitors block is disabled and is not being shown to other users.
-
trevorgooch started following jcogdell
-
You should be good to go once you have made the edit with the weight in grams, no need to rename the symbol again. On the connector, currently the data record connector field isn't connected to anything in the OIP, so you would either have to use the drop down everytime you insert the symbol or configure the symbol how you want and then save it as a 'red symbol' by using the convert to plugin check box in the create symbol command dialogue. or add a consumer electrical component to the symbol definition in the resource manager with the correct connector and power data
-
What units did you use when entering the data in the record? you need to use grams for the hoist weight and mm for the chain length
-
The total weight includes the complete 24m of chain, its calculated based on the values entered in the data record. It should be a fixed value based on (the max chain length x weight per meter of the chain) + weight of the body of the hoist.
-
Onl yrename it once, as long as the new name isn't the same as the original from the Vectorworks library it should be fine
-
@Peter Telleman You have to edit the hoist symbols attached data record in the resource manager once you have imported it. Make sure to rename it and save it into your workgroup or user library. If you don't rename it then whenever the original hoist from the default libraries is used it will overwrite any edits or changes you have made to the symbol. Heres a copy of one of my hoist libraries with both 18m and 24m hoistsMetric Hoists.vwx
-
@zoomer Is correct, the resource manager displays anything in the workgroup folder location where as th resource selector for performance reasons is set to look in a specififc location in the workgroup folder set by the tool that the resource selector is part of. This is partially for performance and partially for workflow speed so that the tool filters to the correct libraries each time.
-
Hi @Stefan B. This is definetly a bug with the resource manager, I can verify that I'm having the same issue. It looks like it only affects the resource manager though so if you use the resource selector in the hoist tool it will insert the chosen host type correctly. I'll get a bug report opened
-
I've heard back from them and its on their priority list but currently there no time frame available. When I hear anything further, I'll let you know
-
I've reached out L-Acoustics and will let you know when I hear anything
-
It may be that the glitch is saved into the document VGM cache, that is used to speed up 3D perfomance. You can reset this by going into your document preferences, uncheck save vgm graphic cache in the display tab and then change between a 2D top plan view and a 3D view. This will force Vectorworks to redraw the 3D geometry from scratch, rather than use what is in the cache.
-
there are 2 options, Deleting the file from the application library folder, however since the library will be reinstalled with every update, you'll have to do this again each update. The better option is to open the original library file in the application library and use the manage bridle parts dialogue to uncheck all the imperial parts in the use column. save back to the original location. Then update you application preferences (in this case the xml file in the user folder) by opening an empty file and hitting the update button in the bridle parts manager. This requires a bit more work upfront but you shouldn't have to worry about any content updates, and has the added benefet that the imperial parts will still be available if you need to coordinate with a US rigging team or production, they just won't be used automatically by tool to configure bridles.
-
The xml and the bridle part library are 2 seperate things. The library is a user editable vwx that stores all the bridle part symbols and their basic data, this is what users should be editing and customising to control their own bridle part libraries. Normal workflow is that this will replace the default bridle part library once edited and saved into either a user or workgroup library as described above. As far as I know the xml is created by the Bridle parts manager whenever it is used to edit the bridle parts library, and will be over written everytime the manager is used. This stores the application availability of parts from the library based on editing the vwx library file (important to note not the curretn show file). Because this is application preferences this is stored in the user library folder and should not be moved or manually edited.
-
Plug-in objects do not retain assigned class information
jcogdell replied to LJW Design's question in Troubleshooting
Currently this is normal behaviour in Spotlight except for the few(lighting devices, trusses, etc...) object types with autoclassing options in the Spotlight settings. Personaly I would like to see more auto-classing options for Spotlight objects and have added it to our internal feature road mapping. My prefered solution to deal with this when drawing, is to have a number of saved views set up in my template file for drawing specific things like power cables or Distributors, that way I can activate a saved view to quickly set the active class and layer. -
@LJW Design The EntEquipUniversal data record is auto-populated using the Data manager, this is why you lose the data added to the record in the symbol definition. Most of the record fields are linked directly to Spotlight object parameters and will actively update as your design progresses and the parameters in the object data gets filled in or edited. Maybe @Scott C. Parker can provide a bit more info about this, as the Data manger is a part of the software I'm not really up to speed on.
-
Composite Racks and vertical slots
jcogdell replied to Andrew.Stansfield's question in Wishlist - Feature and Content Requests
Hi @Andrew.Stansfield Is this related to ConnectCAD rack planning? To clarify part 2 can you post a picture of the rack configuration to help show our dev team what you are wanting? This'll help me put an enhancement request into our system for the ConnectCAD team.