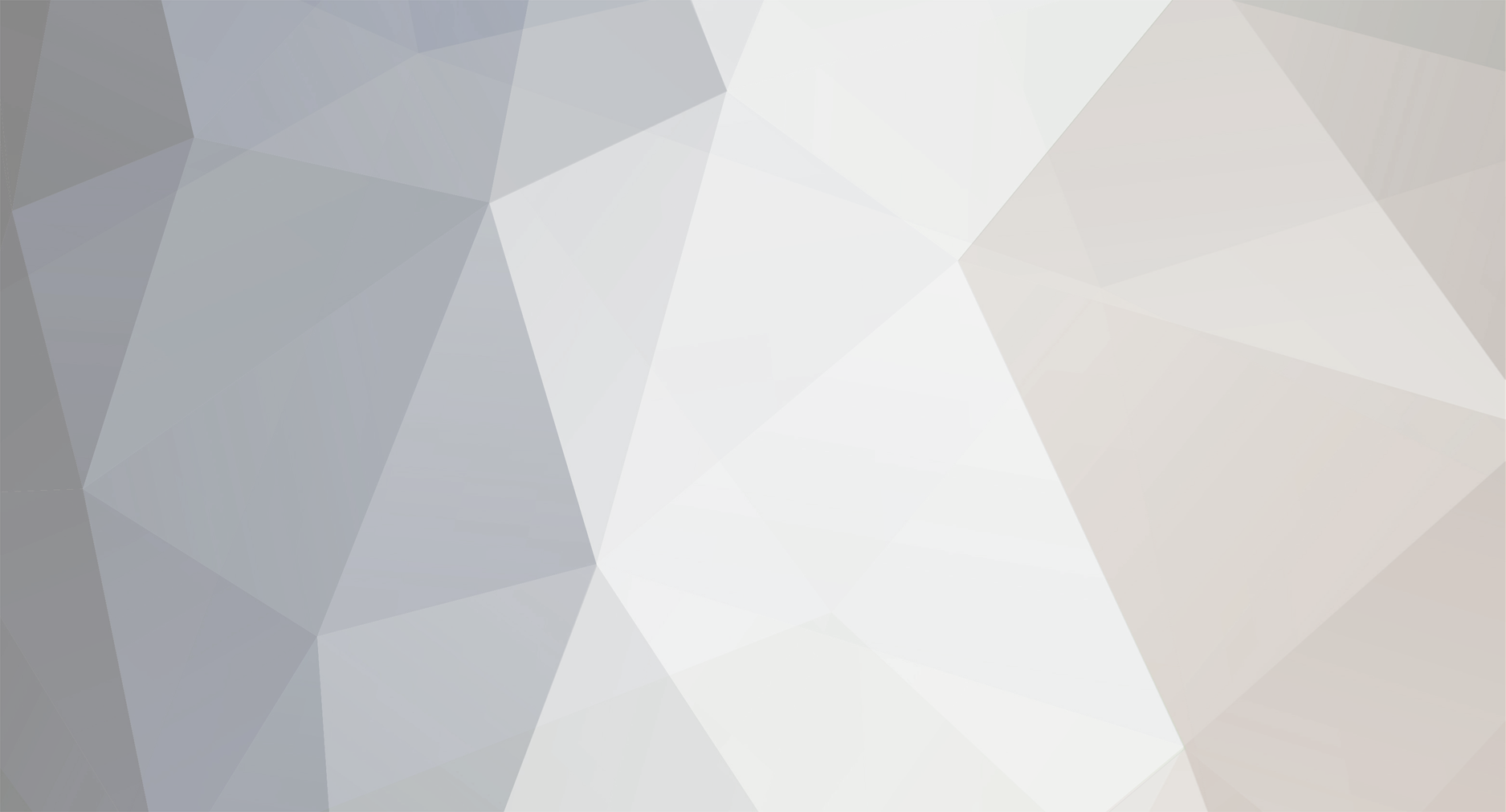
jcogdell
Vectorworks, Inc Employee-
Posts
960 -
Joined
-
Last visited
Content Type
Profiles
Forums
Events
Articles
Marionette
Store
Everything posted by jcogdell
-
This is a known issue and has been brought to the dev teams attention. As far as I can tell it is a display issue and doesn't affect the Braceworks calculation results. I'll bump the bug report
-
The system check command doesn't do a braceworks calculation, it only checks that the system is ready for calculation by looking for errors like disconnected hoists or lights. You need to run a full Braceworks calculation for the system to calculate the loads on each hoist and hanging point.
-
I've had a look through you file and have figured out what is going on, After I cleared the calculation results and ran a full Braceworks calculation, not the check system command the truss calculates correctly. The check system command is not a full Braceworks calculation, its meant to be used to check whether your system is ready for a Braceworks calculation by looking for unsupported elements, disconnected hoists and other 'physical' errors in the system, that would prevent the system from calculating. This means the command will not do any force/weight calculations or produce any results related to them, such as force lines, hoist loading and heatmaps.
-
Can you DM me the file so I can take a look?
-
Did you change the trim heights of the hanging positions after connecting the hoists by changing the Z coord? Once the hoists are attached you need to use the change trim height command to keep the hoists attached when you change the trim height. You can also use the change system trim height button in the OIP, to check whether the hosts are correctly connected. in the change trim height dialogue, set the the change drop-down to entire system, then everything that is connected will be highlighted enabling you to see if any of the hoists aren't connected to the trusses correctly. Otherwise what does the calculation overview errors and warning section say? If the hoists have become disconnected then you will need to re snap them to the trusses, you can do this by dragging them to the side and then back onto the truss if the drops are disconnected then you will need to re-insert them with the insert connection tool or the insert drops command Also if possible try not to convert your trusses to hanging positions when you are are planning rigging, it can cause problems such as not being able to identify or display the trim height of the trusses inside the hanging position. If you are doing this to give the trusses a name, you can use the position name field in the truss properties instead and use a data tag to label them, there are a number of different tag styles in the library for this. Also any light or other spotlight object hung from the truss will have the trusses position name pushed into its position field, the same as if it was hung from a hanging position.
-
use the change trim height of system command in the truss object properties, this will move the entire truss line and adjust the trim height of the hoists without disconnecting anything
-
Hi Jean Look on the Vectorworks university for the Cable tools learning path, it covers most of the cable planning related workflow. The only thing to be aware of is that the video about cable paths needs to be updated as there have been some changes since it was created.
-
There are a number of Hoist data tags in the annotations>entertainment folder of the Vectorworks library. Double clicking on one will activate the insertion tool. You can add tags as labels to hoists on the design layer or in viewport annotations. The nice thing about using them in viewport annotations is that each viewport can have different tags on your hoists without needing to edit class and layer visibility or your design. You can also customise the data tags from the library
-
Once inserted drops (hoist or dead-hang bridle) can't be moved, so you have to make sure that they are in the correct position at insertion. Moving them after insertion will disconnect them and you will need to reinsert them with the insert connection tool
-
changing lighting instrument color by class VW2018
jcogdell replied to Rebecca 9's question in Troubleshooting
I'm not sure if this is possible in 2018, its definitely doable in newer versions of Spotlight, look in file menu > Document preferences > Spotlight Settings open the Lighting devices Classes and Colors pane turn on Modify lighting device color and set the preferences for how you want it to work You will also need to make sure the class you assign the lights to has the correct settings as well -
Also check your Braceworks calculation settings, do you have a safety factor applied? is compensate drops on? What version of Spotlight are you using?
-
Unless you are planning to use custom built circular trusses use the standard truss tool with manufacturer based curved truss sections, that should avoid the problem
-
Does the circular truss have a weight, there is a known issue at the moment where if you don't define a circular trusses weight at creation it can't changed later, this will prevent a successful calculation. Otherwise as far as i can tell a my end it is working correctly and I can attach a distributed load. The only tricky thing is that the distributed load tool only draws straight lines so you need to be careful to draw in small segments that stay within the trusses geometry. if this doesn't help or you continue to have problems please post a file and I'll have a look
-
export MVR creates GDTF data with not correct dmx footprint
jcogdell replied to EJ Berendsen's topic in Entertainment
Hi EJ Unless you manually link a GDTF to your fixtures in Spotlight there will not be a valid GDTF in the MVR export. Any GDTF that begins with 'Custom@*********' is a place holder to tell the receiving software that there is a fixture but the GDTF itself doesn't contain any data about the light. This is likely why the GDTF is displaying the wrong dmx footprint To link a GDTF you first need to go to the GDTF share website and download the ones you want, then use the Import GDTF command to import them into your active file resources (or into a user or workgroup library so they are available for future projects). Once you have the GDTF in your active file resources you use the GDTF fixture mode drop-down in the lighting device properties to link the GDTF to the light and choose the mode you wish to use. You can now run the export MVR command and the GDTF's will be automatically included. Using the fixture mode parameter will only assign a Vision lit file to the light for export to Vision, not a GDTF. There is a workflow doc on the Vectorworks university that goes into more detail about the GDTF and MVR workflow, its focused on using MVR with Vision but its the same workflow on the Spotlight side no matter what your destination software is. https://university.vectorworks.net/mod/scorm/player.php?a=373¤torg=articulate_rise&scoid=746 -
export MVR creates GDTF data with not correct dmx footprint
jcogdell replied to EJ Berendsen's topic in Entertainment
Where did you get the GDTF for the color strike from? It's not on the GDTF share website Since its not from the manufacturer section of the share there's a good chance that it has errors in it. Also what are you using to open the MVR? At this point most other CAD and Privis applications do not use the GDTF part of the MVR standard and instead you have to link the GDTF to one of the opening applications internal fixture definition/ profiles. This means that its possible that the error is not in what Spotlight is exporting but in the receiving application. without more info or a sample file I can't say for certain whether the problem is with Spotlight or somewhere else (like the GDTF or receiving application) -
I had a quick look at your file and as far as I tell the reason it is taking so long is that the DWG to VWX import process is trying to import 91000+objects in to the active file resources. This not only affects the import speed but will have an enormous impact on the performance of your Spotlight file afterwords as well. Do you need the entire file? If there are only specific parts of the DWG that you need restrict your import to only those parts, either by saving a DWG with only the part of the file you need or by using the Import dwg dialogue class/layer controls
-
Attaching fixture to truss causes truss to become invalid?
jcogdell replied to scottmoore's topic in Braceworks
You should be able to snap the light to either lower chord of the truss. The trick is to hover the mouse just outside of the truss, the insertion preview should them correctly display the light on the chord. The light will only snap to the center line if the auto-connect highlight triggers. I find using the simplified truss view with the rest of the truss geometry turned off makes this much easier to do, since it reduces the number of snapping targets -
Best practices for responsive files and small files sizes?
jcogdell replied to Wood's topic in Entertainment
@Tom W. My understanding (I could be wrong though) is that the reorganization only changed the layout of the library folders to make it easier for to locate symbols but didn't change any of the basic behaviour of the resource manager. -
Best practices for responsive files and small files sizes?
jcogdell replied to Wood's topic in Entertainment
Another thing that can have a huge performance impact is DWG importing, a common problem for entertainment users is that many venue plans are provided only as very poorly drawn DWG's which even when the correct import settings are used can result in thousands of individual line based objects in your file. Typical issues include groups that contain multiple layers of grouped geometry, making it hard to identify just how many objects have been created during the import process, even with the correct import settings not all DWG's include nicely ordered/drawn blocks Where possible always use a shuttle file when importing DWG's, so you can experiment with the import settings and simplify the file before bringing it in to your main project or template file. The use of favorite files can also have a big performance impact, the larger these files are and more of them you have, the slower the resource manager and tool resource selectors will perform. While this may not be a direct file related issue it can have a large impact on your drawing speed since you will constantly be waiting for these dialogues to react. The root cause is that favorites files are auto indexed and refreshed by the resource manager every-time you open the manager/selector. The solution is to keep only a few small favorite files and instead use your user and workgroup folders to store any large custom libraries or content files as these will only get indexed when you manually refresh the resource manager libraries. -
Normally the 3D component of the symbol contains the emitter, not the 2D component. This means that if you wish you can create a 2D element that displays as if it is in your desired out-rigged orientation without needing to change the emitter in the 3D component. You can then, if you need or want to, focus the light separately for 3D work (using focus points, the pan tilt parameters etc...), as long as the automatically focus 2D setting in the Spotlight document settings is turned off.
-
Connecting a single hoist to a vertical truss
jcogdell replied to Mathijs van Ommen's topic in Braceworks
This is a hard coded safety restriction in Braceworks, The easiest workaround is to attach a point load object to the prerig truss your vertical truss is going to hang from and use that instead of the hoist and vertical truss in your calculation. Another option is to add a T corner to the top of vertical truss so you can attach a second hoist or drop to support it -
Not without breaking the connection to the soca cable. You can disconnect the cable by using the reshape command or by double clicking on the cable To help me understand your workflow, why do you need to move the breakout?
-
You need to tag the Breakout or plug box at the end of the soca cable not the cable itself. There are a number of sample data tags for this in the default tag library
-
Also turn off textures and color in the shaded view options.