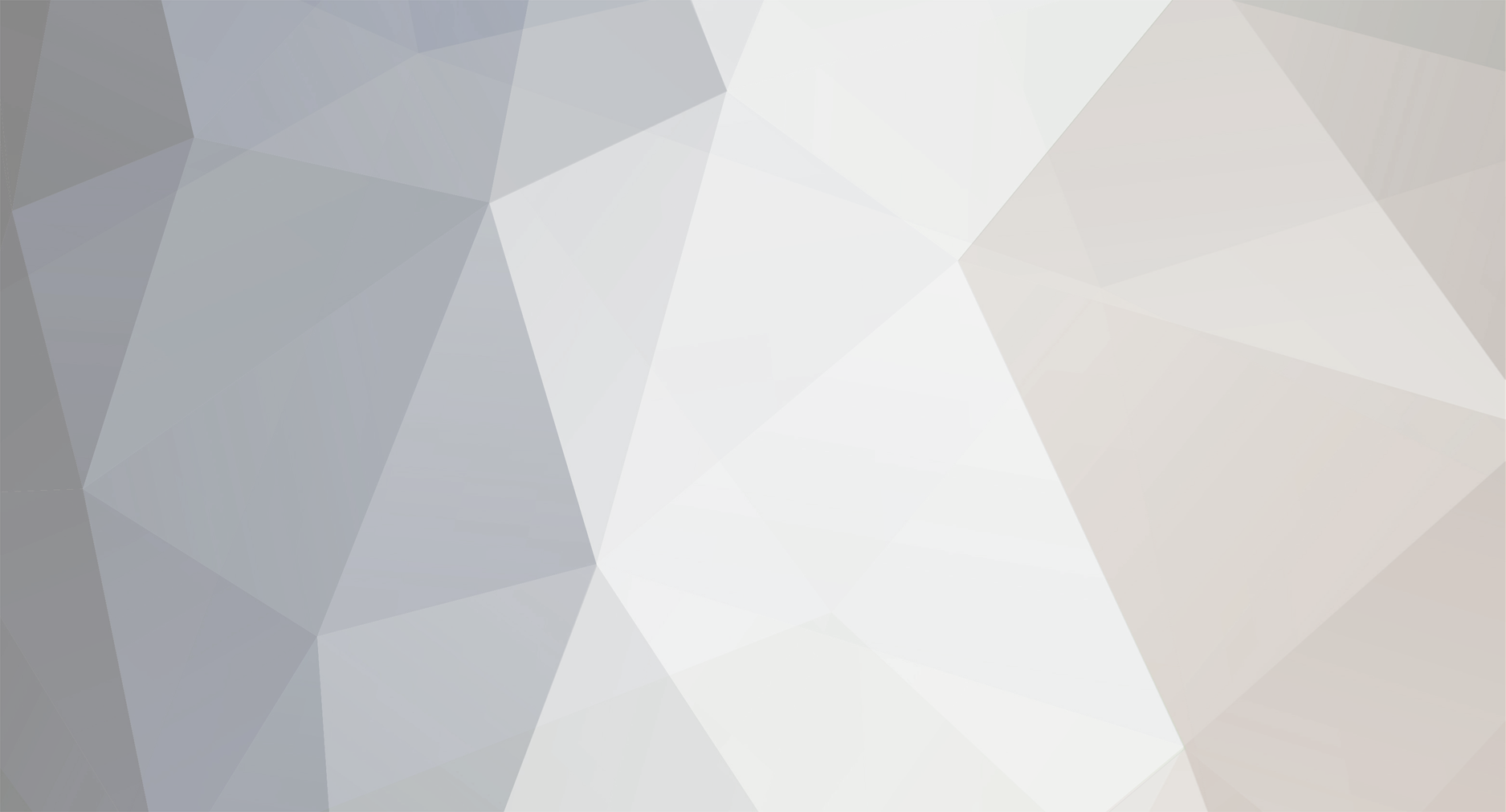
GWS
Member-
Posts
630 -
Joined
-
Last visited
Content Type
Profiles
Forums
Events
Articles
Marionette
Store
Everything posted by GWS
-
I use 'convert to lines' - hidden line option. Pick the view that you require, i.e. front, right etc and then convert. you may have to compose the individual lines into single polylines by selecting the lines and using the compose command.
-
It sounds like you're orientating you objects so that you're looking at it's front view but in VW's top/plan view, hence when you switch to right or left view the closet is lying on it's side. At least I think that's what you mean. You need to rotate your closet so that the front view is the VW front view. I would do this by selecting different views, say top view and/or right view and rotating the closet (cmd-L) to be the coresponding view in VW. (see PDF) I may have misunderstood you, so apologies if that is the case. Can you post a file so there is a better inderstanding of what you mean?
-
I've not done a great deal but when I have used 3D printers they've normally required STL files. VW seems to export these fine and I've had good results normally with fairly small objects that are made up of solids (extrudes, subtractions/additions etc). I have had issues with lofted surfaces, which seem to remain as surfaces whatever I do even though the surfaces make up a 'tight' solid, consequently the printer does not recognise them as solid and so will not print them. The work around that worked for me was to export to Inventor which converted the surfaces into solids without any further adjustment other than the import command. I would imagine that if the printer accepted 3DS files you might have better luck with that sort of conversion/export. As far as scale is concerned I exported 1:1, I always try to keep the prospective problems to a minimum!!!
-
I set the render to custom renderworks and the same result occured, only when I turned of ray tracing did the jagged edge disappear....very strange. Why would ray tracing cause such an effect?
-
Useful additions?
GWS replied to VincentCuclair's question in Wishlist - Feature and Content Requests
Agreed! -
Useful additions?
GWS replied to VincentCuclair's question in Wishlist - Feature and Content Requests
I think i'm right in saying that your point 4 does already exist. If you batch export the sheet layers and also click on the 'export as seperate files' button (bottom right of the dialogue window) you will get the sheet layer names. -
I've not heard a good word about it yet!!!
-
Further more, I have just installed a version of Cubase, virtual studio music software, and they use software called 'License Cotrol Software'...I wonder if there is any mileage in that for getting rid of the blessed dongle....!
-
VW is the only software I use that needs a dongle and I too worry about the cost of replacement. I haven't lost one yet.....(whoops now I've done it) but I would not want to have to re-buy the license again because of absent mindedness. There must be another way, surely.
-
I find complicated paths when using the EAP command often cause a 'failure'. Splitting the path is a real pain but can often help. I was hoping parasolids would help this, and it has, but only a bit.
-
P.S. I am running Alibre through Parallels and so far it has worked extremely well.
-
Since posting this I have been looking at the 30 day demo which was very interesting. It appears to be very similar in its ways to Solidworks and as the price seemed very favourable I have also bought the standard version. I haven't explored the more advanced modelling side yet but I was able to create a mechanism and 'proof' it's mechanical movements fairly easily. The tutorials are also very useful. There is lofting and more 'creative' 3D operations and, what is called, 3D sketching which I haven't got to yet but from what I have seen Alibre Design does fill a gap for mechanical design for a very affordable price. I would say it's worth taking a stab. I also imported an IGES file from VW which worked very well indeed. I'll keep you posted.
-
I came across this just the other day. I was only rendering in Open GL with a simple image imported as a texture onto a sphere but it wouldn't show up until I changed from "active only" to one of the "show other...." options. What I finally discovered was that the render has some connection with the "None" class and unless "None" is turned on the render would not show correctly. Try setting the class visiblity to one of the "show....." options but turn off the classes you don't need and leave "None" turned on. I hope this helps.
-
3D Modelling - Other than Architecture?
GWS replied to Kevin McAllister's topic in General Discussion
a note on the Bond theme: While the art department may well use VW I know that the Special Effects side, the guy's that design and build the mechanical rigs, use Solidworks and VW just isn't up to the job of mechanical design. I also use VW in the entertainment industry but the options offered in the mechanical area are not sufficient (PIO's in the form of bearings, nuts & bolts and other hardware do not make the jump required). After using VW for a long time too I, sadly, am having to look elsewhere for the necessary design tools to keep up with my industry. -
If you set the text size from the drop down menu before selecting the dimension tool the size of the text should be adjusted for all future dimensions.
-
Good to know there are others out there with the same problem
-
I have the same problem when editing solids, the editable objects appear displaced and I can't select them. This often happens when changing views while in the edit mode. I also have problems with PIO's re-setting themselves parallel to the ground plane and I have a feeling that this is connected. I have asked about this before but either nobody else has experienced it or there is no solution. If you find the problem, and a solution, I'd be eternally grateful. This only started happening after I upgraded to 2009 and beyond so it maybe something to do with the parasolid side of things....I don't know. What I do know is that it is extremely to frustrating and slows down the workflow inordinately.
-
3D fillet, dimensions and constraints.
GWS posted a question in Wishlist - Feature and Content Requests
This is becoming a yearly custom but hear goes. Please fix the 3D fillet/chamfer tool so that it is included in the history and it doesn't have to be ungrouped and then re-applied when editing. Please introduce proper 3D dimensions (not just for walls, I find I don't use many walls with machine design, in fact why are they even included in MD) Please introduce 3D contraints (similar to a "mates" system in other programs) to allow 3D movement of a mechanism. Surely price cannot not still be an issue, I have just discovered a program that does this and the standard version only costs ?89!!!!!!! Thank you for you consideration. P.S. I know that VW is mainly used by Architects but please spare a thought for the engineer. -
Dimension values in non-2D Plan
GWS replied to wvancampen's question in Wishlist - Feature and Content Requests
Once again I'd like to add my frustrations to this item. It seems that almost every other CAD software has this. -
Yes the viewer can do open GL, I don't know about other render modes
-
I have just come across this software which seems amazingly cheap and from a mechanical point of view quite useful. Has anyone else used this and is it any good. How does it compare to VW?
-
Unable to use the radial dimension tool on cylinders in plan view
GWS replied to ChrisW's topic in General Discussion
Solidworks and Inventor seem to be able to do it!!!! -
That's just what I do and it works well for me. It keeps the drawing organised and also means that when rendering you can easily turn off certain classes such as 'Bearings' (which may be internal and therefore not needed when rendering a finished view).
-
Thank you Tim, I'll give it a look
-
Hi Francois, I have exported the attached file to STL and then 3D printed it. It all worked fine, except that the grey surfaces would not read as a solid. (I have cut away half of the surfaces to show that they are hollow). I could not find a away to get them to be read by the 3D printer as a solid. I eventually imported the STL into 'Inventor' which read them as a solid and then exported again to the printer. I have used other files with great success but every now and then VW doesn't quite join the dots. HTH