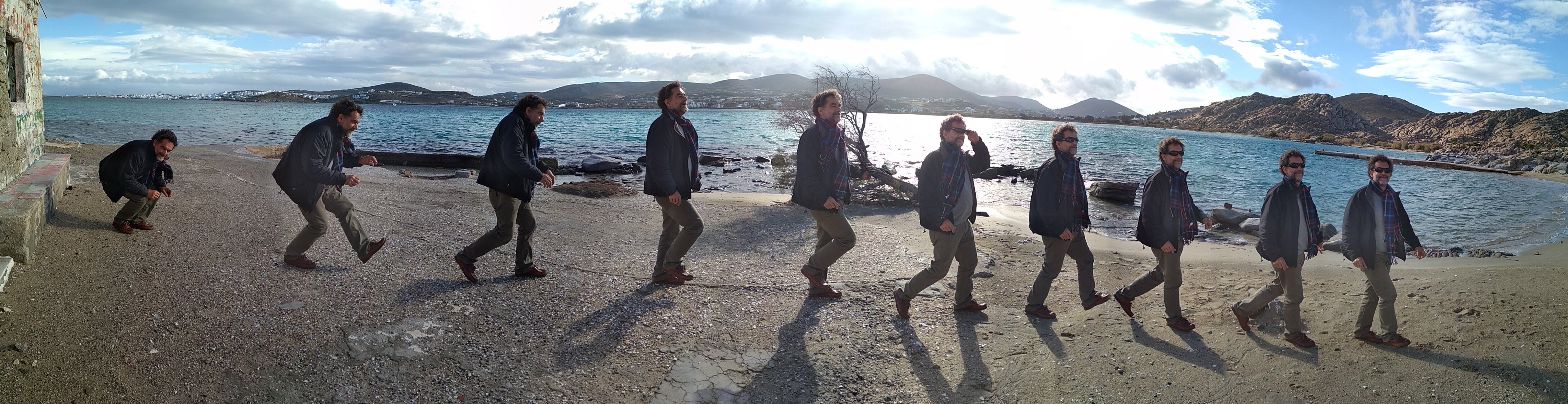
Conrad Preen
-
Posts
1,023 -
Joined
-
Last visited
Content Type
Profiles
Forums
Events
Articles
Marionette
Store
Posts posted by Conrad Preen
-
-
@Thomas Peters We will be working on that topic. Meanwhile brute force is always a way forward !!!
C
-
More efficient than...?
Anyway yes, we have this on our list of things to consider. Bear with us a little. This is something that needs to be properly thought through not rushed into production only to discover the problems later. In the end it isn't such a big deal to put a drop point as a named location for a little while longer?
Conrad
-
No, but there are other exciting things in the pipeline 🙂
Haven't forgotten though.
C
-
@Dhargrove Let me read back to you to make sure I've got this right. You have 2 Vectorworks documents - correct?
If that's the case the short answer is that 2 documents can't communicate unless they are both open. I looked into this idea years ago and it doesn't offer anything better than having a single master document plus project sharing. Viewports let you present the same object in different contexts avoiding the need for special mechanisms to keep stuff in sync. You'll find lot's of info on project sharing in the Vectorworks help.
Best
Conrad
-
Yeah in essence drop points are a promise to place future equipment. We need them for when the future has yet to arrive. They are also a node shared between separate equipment located at the same place. But they are not equipment. A drop point could be just a hole in a wall with a coil of cable emerging - that doesn't belong in your equipment reports!
On the other hand ConnectCAD is about saving you time, so we don't like the idea of making you place a drop point in order to add equipment that you already know about.
But if you think of a drop point as a named location then it doesn't seem unreasonable that it should be different from the equipment at that location...
These are the kind of questions that keep me awake at night 🙂
Conrad
-
You could save the configuration (Rack + Data Tags) as a symbol - you'll need to experiment a bit but I suspect Convert To Group would be the way to go. Then you can just drag it on from the Resource Manager and un-group it. Sharing symbols with your colleagues is easy. Just set up a shared document on your network and add the resources in their. In the Resource Manager set up a Favorite pointing to this and you're done.
Hope this helps.
Conrad
-
Hello @Caveman
Regarding extra data for your racks, the way to go is to create your own record format and attach it to your rack. You can use the Data Manager to automate this so that every time you create a rack your record is attached. Data Tags are the best way to visualise attached records. You can set them up exactly the way you want. I'm really loath to add anything but the basic name text to racks. The experience with equipment items has shown that however much effort we put in to providing a solution that will "just work" there's always someone who has a problem. So moving forward we will just create some example data tags in content which will work for most people.So, on to front and rear views. We're moving towards modeling all the physical layouts in 3D to provide a cleaner data model. That means using viewports to present front and rear views. Creation of viewports can be automated just like everything else in Vectorworks. So I would strongly suggest not duplicating racks but instead get into scripting those operations that you find yourself doing repeatedly using Marionette, Python or Vectorscript. I know it's a bit of learning curve but the pay-off is huge.
Best
Conrad
-
Hi @spettitt
The Device Builder ought to round the width up to the nearest snap grid. Filing a bug now.
Conrad
-
1
-
-
On 1/6/2022 at 12:27 PM, tspilman said:
My questions are as follows:
Will this 2 into 1 connector work?
I cannot work out how to define the connector on the other side of the panel (take '.01'; the cable to the right should be OPTICON; the cable to the left should be LCDUP)
Hi @tspilman Tim,
a) ConnectCAD won't stop you from connection 2 into 1
b) You would have to define this connector panel in a different way. Let's rewind a bit. In ConnectCAD's we concern ourselves with the connector on the cable - not the chassis connector on the device. That's so we don't have to worry about what mates with what. The connector type is stored in the socket and that information is read by the circuit object. So where one side of the panel accepts an OPTICON and the other side an LCDUP then you'll need device with 2 sockets to model this panel port on a schematic. A way to go would be to base such a device on our standard jackfield devices and change the connectors.
Hope this helps a bit.
Conrad
-
Thanks for the update George! And for sharing this with the community!
-
@btgroves it's a bug - thanks for reporting!
-
Hi @joster
You can use the 3D Rack object to visualize the layout of your console bays to a higher degree of accuracy. The way to go is to drag your equipment into standard 2D rack objects without worrying too much about what they look like. Then elsewhere place a 3D Rack object for each of the 2D Racks and assign each 3D Rack to it's corresponding 2D Rack using the popup in the Object Info Palette ( easier to do than to describe !!! ).
Now again in the OIP set the rack style to Console, set the slope of the bay, set the width of the side panels and you get a barebones rack-mounting space that displays your equipment. Insert that into the models created by your console builder and you're done.
Best
Conrad
-
1
-
-
@btgroves We have no plans to remove this feature. However I do urge you to check out Niko's demo of how to use the Data Manager to automatically add any record you like to every new device. You have to scroll down a bit to find it . Maybe you will like this better...
-
1
-
-
-
@spettitt Yes I've come across a few of those in my time... but I was always grateful of that extra 1/2U to let the equipment breathe a bit.
Conrad
-
-
1
-
-
Hi Daniel,
Yes I'm seeing that when I try using the imperial template. I'll file a bug.
Conrad -
@Dendecko It does work, I just tried it now. You'll just need to include the Socket.tag parameter in your report and you'll have to change both the Name and Tag.
The reason Devices and Sockets have separate name and display tag parameters is because on drawings you need to save space while in reports and lists you need longer more descriptive naming because you don't have the visual context.
-
@SAmmerman It's always the same at this time of year. The questions we get are 90% stuff that is about to change for the better 🙂.
I understand your frustration. However in the last 20 years no-one else has raised this issue. The way DA's are drawn is pretty standard, and it's useful to be able to quickly set the number of outputs. That doesn't mean that I don't want to accommodate your wishes, but I also have to consider all the other users too and prioritize the use of limited resources.
I've noted these points as matters to be improved.
Conrad
-
1
-
-
@btgroves Just want to point out that there are better ways now to add extra info to ConnectCAD objects. You can automatically attach your own records and display their values. But you probably know that. We will continue to support the old way but I want to encourage everyone to go towards attached records.
Regarding your question, do you want to PM your CustomParams.txt file and the exact steps you took and I'll look into it?Conrad
-
Maybe try using worksheet reports - just a suggestion - I haven't tried it.
Conrad
-
1
-
-
@wscooperWe will get to this as well. It's a question of hours in the day.
-
@wscooper I agree that we don't have a specific model for multicore cables and right now we leave this up to the user. In the interests of simplicity we have sort of merged the physical cable with the the signal connection. I am very conscious of how intimidating ConnectCAD can already be for the new user so I want to be very careful about adding yet more complexity. I hear you but I'm searching for a solution that will keep simple things simple.
Conrad
-
@SAmmerman Interesting food for thought. Just to give you perspective, we have to tread a fine line between having a feature-rich product and one that is simple enough for a new user to get useful work done in less than a week. The learning curve is massively important.
So now some answers:
1) you do not have to use our DA tool. You can create your own devices with the sockets laid out the way you want them. Nothing constrains you to rectangular boxes either. You can use any graphics you like inside a ConnectCAD device. You only have to create the device your way once - just click the Save as Symbol button to keep it and share it to other documents using the Resource Manager.
2) Well that's an idea. But maybe even better just allow the Prefix to have a numeric suffix that determines the starting socket number. Say the Prefix entry is PORT05 then the series created would be PORT05, PORT06, PORT07... formatting and start number in one go without any extra UI.
Conrad
-
3
-
Edit Cabling Locks Up
in ConnectCAD
Posted
@ktucker Hi Kevin, thanks for reporting this and sharing the file with us. It's an interesting (and realistic) case where a very large number of alternative routes exist from a given drop point but without all of these being necessarily relevant. We will fix the overload issue in the next service pack and I'll give some thought to how we can further optimize these calculations.
Conrad