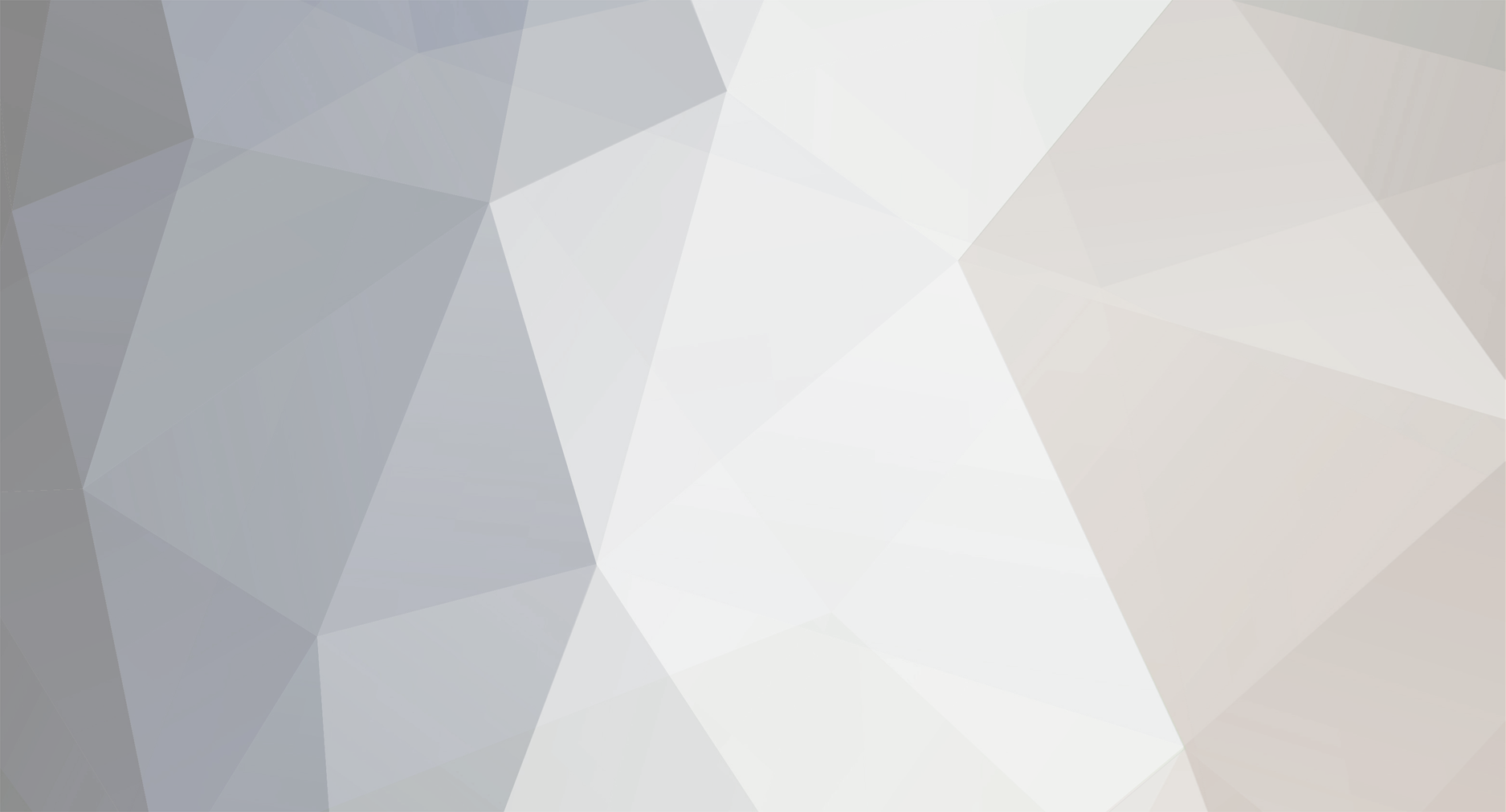
axhake
Member-
Posts
92 -
Joined
-
Last visited
Reputation
46 GreatPersonal Information
-
Occupation
CAD & Data Manager
-
Location
United Kingdom
Recent Profile Visitors
2,570 profile views
-
Tobias Kern started following axhake
-
Hi @AlanW spent most of the afternoon trying to figure the RGB value and came to the same conclusion you did about it being 16-bit. I am trying to create some classes for a project I am working on and they define the layer names, pen thickness colour etc which they provide in excel format to be imported. Unfortunately VW cant import so was trying marionette to see if I could do it that way and create the layers as classes which I have done thanks to @DomCnode "XLS GetValues" which works nicely for extracting the relevant values from the excel file to create the class names. What I have been trying for the last few hours is to be able to set the class "Pen" and "Fill" colors using the "Set Pen Color" and "Set Fill Color" nodes with little success 😒 Do you have an example of how you manages to get the RGB color values to work?
-
Stories not appearing in the right place in referenced file
axhake replied to sjennison's question in Troubleshooting
Have had the same problem, only just received a reply from VW Support. When referencing a VW file (A) into another VW file (B) to create the drawing sheets you need to replicate all "Stories" need to be replicated in (B) to match the "Stories" settings in (A). You need to detach the reference model (A) and then reattach the reference file (A) again for everything to display correctly. From VW Support: "Im afraid this is working as intended as there isn't a way of referencing or importing story settings from one file to another. We do recommend for users to create templates with stories already set up so these can be adjusted when the files are set up. It would be great if we could import stories like we can layers and classes, this has been requested to the developers. " I have found that if referencing using DLV this is not a problem... but have had other problems with grids and text rotating to off angles. -
Section Lines have shifted, Viewport views have stayed the same.
axhake replied to hollister design Studio's question in Troubleshooting
what you could also try is instead of copy/past into a new sheet is: 1. Select the viewport and in the OIP at the top reassign it to another sheet 2. Check and see if the section lines are in the correct place. 3. Update the viewport and again see if the section lines are in the correct position. 4. Switch back to the original sheet and update the viewports on this sheet. 5. Switch back to the new sheet and select the view port and in the OIP move it back to the original sheet. 6. Update all view ports If all is OK you should not have to re do your keynote legend etc. I have had some problems in the past where things didn't look right after some time and tried this and it fixed the issues. -
Section Lines have shifted, Viewport views have stayed the same.
axhake replied to hollister design Studio's question in Troubleshooting
Have you tried moving the plan viewport to a new sheet layer to see if the section lines are retained in their correct position? -
Any time. The best way to learn is through making mistakes... it can be painful but you will remember next time
-
You may want to try deleting the line 59 times! Select the line by fence, in the OIP see how many copies there are
-
Is it possible to share your file so we can see the problem?
-
Have had similar issue before when working with large curves that had been trimmed. If you can select the line try converting it to something else, e.g., a Nurbs Curve, Modify > Convert > Convert to NURBS then see if you can delete it.
-
VW 2018 (and VW2021 and VW2022): Push-pull tool problems continue
axhake replied to line-weight's question in Known Issues
Yes, walls, slabs... and all normal architectural elements. Always have problems when mesh objects are present in the file, thus try and convert to generic solids if possible. I normally have two models open when doing any serious modelling, one where i will model the elements, then when happy will copy and past in place in the clean file and convert to solid, if need to change i go back into the other model and make adjustments and then copy into the other model. I have found that if I'm having problems just selecting objects and Cut, then past in place back into the file sorts some things out. -
VW 2018 (and VW2021 and VW2022): Push-pull tool problems continue
axhake replied to line-weight's question in Known Issues
Hi @line-weight, cant say I have had the same problem, I'm using VW2021 and not experienced this problem. One thing you could check is try changing you snap settings and see if that makes any difference. A little trick regarding BimObjects, they do tend to be over modelled, just like in your example of the server unit case, most people who download only want to see the external shape and do not care to much about what's inside however some people just like modelling and we end up with Bimobjects that come in really bloated. Add onto that they come in as mesh objects. Here is the trick... download your BimObjhect into a blank file, select the object and ... convert to "MESH"... then with it selected convert to "Generic Solid" and see what you get 😀 -
Agreed, show/hide is lightweight and works. I'm from the old days of UNIX where the philosophy was one tool to do one task, worked flawlessly, the more complex you make something the more chances something will go wrong! I was thinking "named selection sets" would be it's own tool, Bentley applications have something similar and like show/hide I find it invaluable when working on complex models. Having the capability of recalling a selection set of selected items can speedup one's workflow.
-
What would be even better would be "named selection sets", much more powerful and flexible. Having the capability to selecting several graphical elements and then to save that selection set for future use.
-
cant say I have found any problems with the scripts, they perform as intended,
-
Orientation X Y Z & Rotate Object in 3D
axhake replied to C.T's question in Wishlist - Feature and Content Requests
- 9 replies
-
- 3
-
-
-
- rotate object 3d
- axis
-
(and 2 more)
Tagged with:
-
Revit, Microstation/AECOsim, AutoCAD... they have all added this functionality to show/hide over the last several years, it's invaluable when modelling complex models