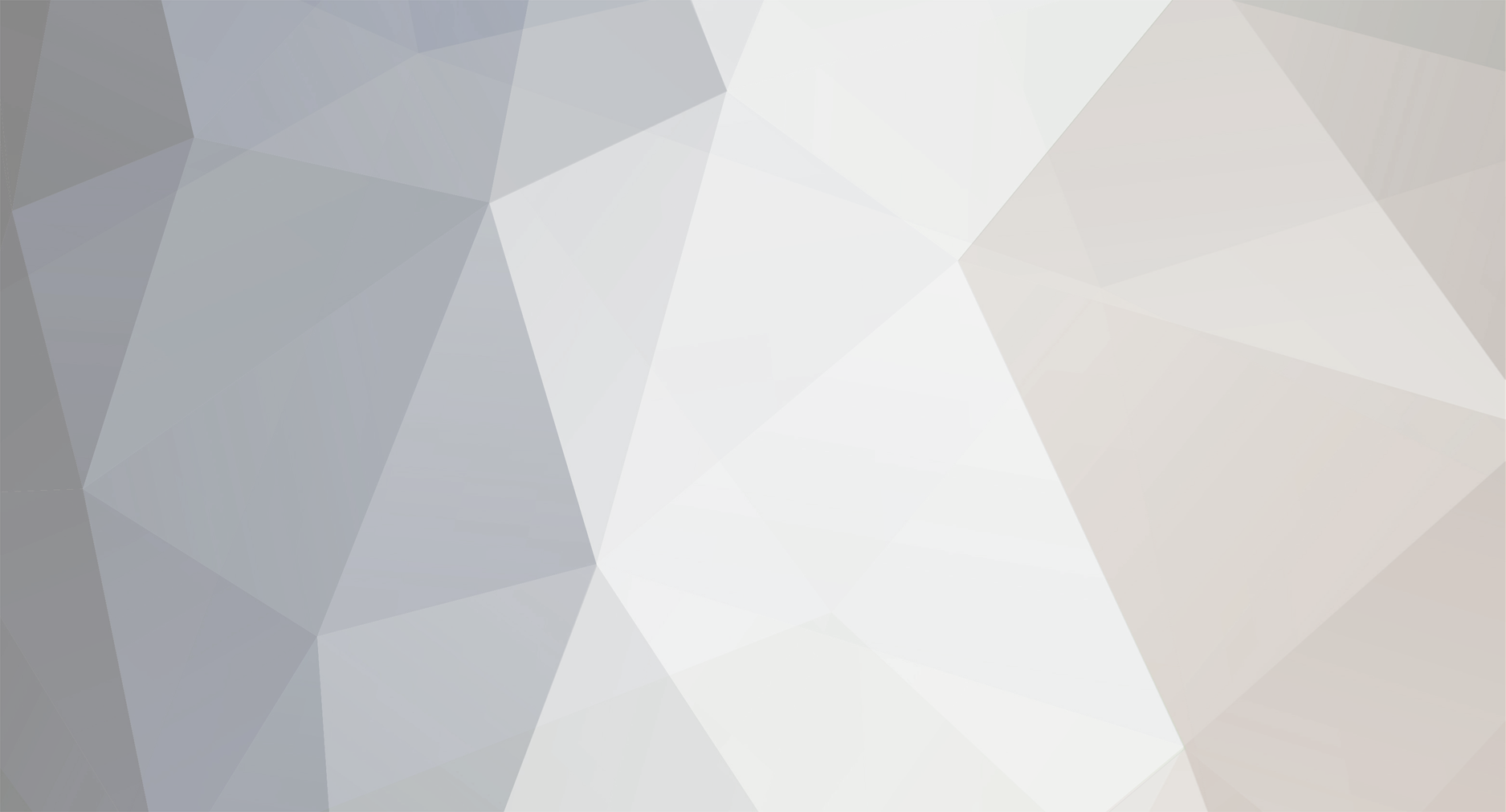
rjtiedeman
Member-
Posts
278 -
Joined
-
Last visited
-
Editing Viewport with Design layer selected CRASHES VW
rjtiedeman replied to rjtiedeman's question in Troubleshooting
Latest update VW 2023 SP7 crashes when opening viewport to design layer. Instantly! Machine is a IMac Pro 3 GHz 10-Core Intel Xeon W. running Mac OS 13.51- 1 reply
-
- 1
-
-
Editing Viewport with Design layer selected CRASHES VW
rjtiedeman posted a question in Troubleshooting
While using VW 2023 SP6 and Editing a Viewport in Sheet Layer with Design layer selected VW CRASHES every time. Going to the design layer and editing is ok. Machine is -Imac Pro 3 GHz 10-Core Intel Xeon W. running Mac OS 13.5 (22G74). Save often!- 1 reply
-
- 1
-
-
Thank you. After seeing the job I determined it was easier to remake the 3D shape than fuss with converting files from a PC. However in the future I will request all 3 formats. The issue will always get back to budget and how much I am willing to do in the name of education. People think “All you have to do“ is push a button and and it’s magic and free.
-
I have had clients ask me what file format they can send me that would include mapped textures. I have successfully imported complex 3D solids as STEP files but have never been able to import a 3d that had mapped graphics unless it was a vectorworks document. Any help would be helpful so I can provide an answer. I have avoided this in the past but the question keeps coming up. The time wasted trying to open files is better spent rebuilding the 3d in vectorworks if possible.
-
What is the best Ipad Pro CAD App that exports to Vectorworks?
rjtiedeman replied to rjtiedeman's topic in General Discussion
No-of course not. I am using VW2023. My old Mac PPC G5 died years ago. I would be happy to have my old Minicad on my Ipad. I have been looking at Sketchup which looks less robust than my old Minicad. -
Thinking about a new monitor - looking for advice.
rjtiedeman replied to Kerschbaumer's topic in Hardware
you can also buy speakers and ignore the monitor speakers. Save your money for a new APPLE DISPLAY. -
Affinity V2 - great companion for Vectorworks
rjtiedeman replied to Jeff Prince's topic in General Discussion
If you look at the Book libraries in Illustrator you will see there are lots color systems. PMS could find it self fading away. I got my first Mac when design companies were still ordering type set from type houses. Type houses disappeared over night along with STAT machines and rubber cement. PMS has been going a long time and most designers have a book at their desk but that could change. If the price gets wacky new standards will arise to fill the void. We will choose the one we can afford. I will probably die from exposure to rubber cement and thinner. -
Vectorworks 8.5.1 (I know its OLD, but I am too)
rjtiedeman replied to Tmarxmiller's question in Troubleshooting
We have VWX lite it’s called Fundamentals. It lacks lots of tools like sectioning, wall tools and many more but works fine for my needs. Side note: When you travel through Europe you have to marvel at the work of architects and builders who built masterpieces with out the aid of computers and software. Those were the days. -
Affinity V2 - great companion for Vectorworks
rjtiedeman replied to Jeff Prince's topic in General Discussion
I just got the notice about upcoming charges for PMS colors. Another $15 per month for pms is not cutting it here. We will just have to get proofs and go back to sending samples via Fedex. They broke the bank. -
Vectorworks 8.5.1 (I know its OLD, but I am too)
rjtiedeman replied to Tmarxmiller's question in Troubleshooting
As I remember Minicad was the only decent CAD software for Mac that you could run or afford. It also had tools that worked like Illustrator, Freehand and others so it was easy to learn. It took 20 years for Autocad to run on the Mac and you have to take a college class to get certified. Really… Sooner later professional software will exceed the cost of what designers can charge or the time needed to learn. -
Vectorworks 8.5.1 (I know its OLD, but I am too)
rjtiedeman replied to Tmarxmiller's question in Troubleshooting
As I remember there was also software called RAM Doubler that could create fake memory using the hard-drive. I used it and it actually worked. -
Did it just become possible to run VW on an iPad Pro??
rjtiedeman replied to Kevin McAllister's topic in General Discussion
Adobe Illustrator CS or something that resembles it runs on my iPad Pro m1 with 1TB SD. The controls are so different from what I am used to on my Mac desktop that it is not that useful for me. It would take relearning tools and key commands that I know by heart. However having a CAD app to record measurements would be a great start. SketchUp for the iPad looks fun. Not sure if the info would translate to Vectorworks. Has anyone tried it? -
Affinity V2 - great companion for Vectorworks
rjtiedeman replied to Jeff Prince's topic in General Discussion
PMS yes. Pantone color chips are essential to controlling printing output. It’s the standard. -
Affinity V2 - great companion for Vectorworks
rjtiedeman replied to Jeff Prince's topic in General Discussion
It would be great to have an alternate option for developing graphic information. So I will see if my clients are interested in experimenting. However we have millions of Adobe documents that we would like to have access to. So if we wanted to break the chains of Adobe domination we would have to leave a lot behind. When a project goes out for production, they go to a Adobe dominated world. It would be like having all houses built with a special Adobe hammer that you had to rent.. It's good that there is another player in the image creation business. I will check it out.