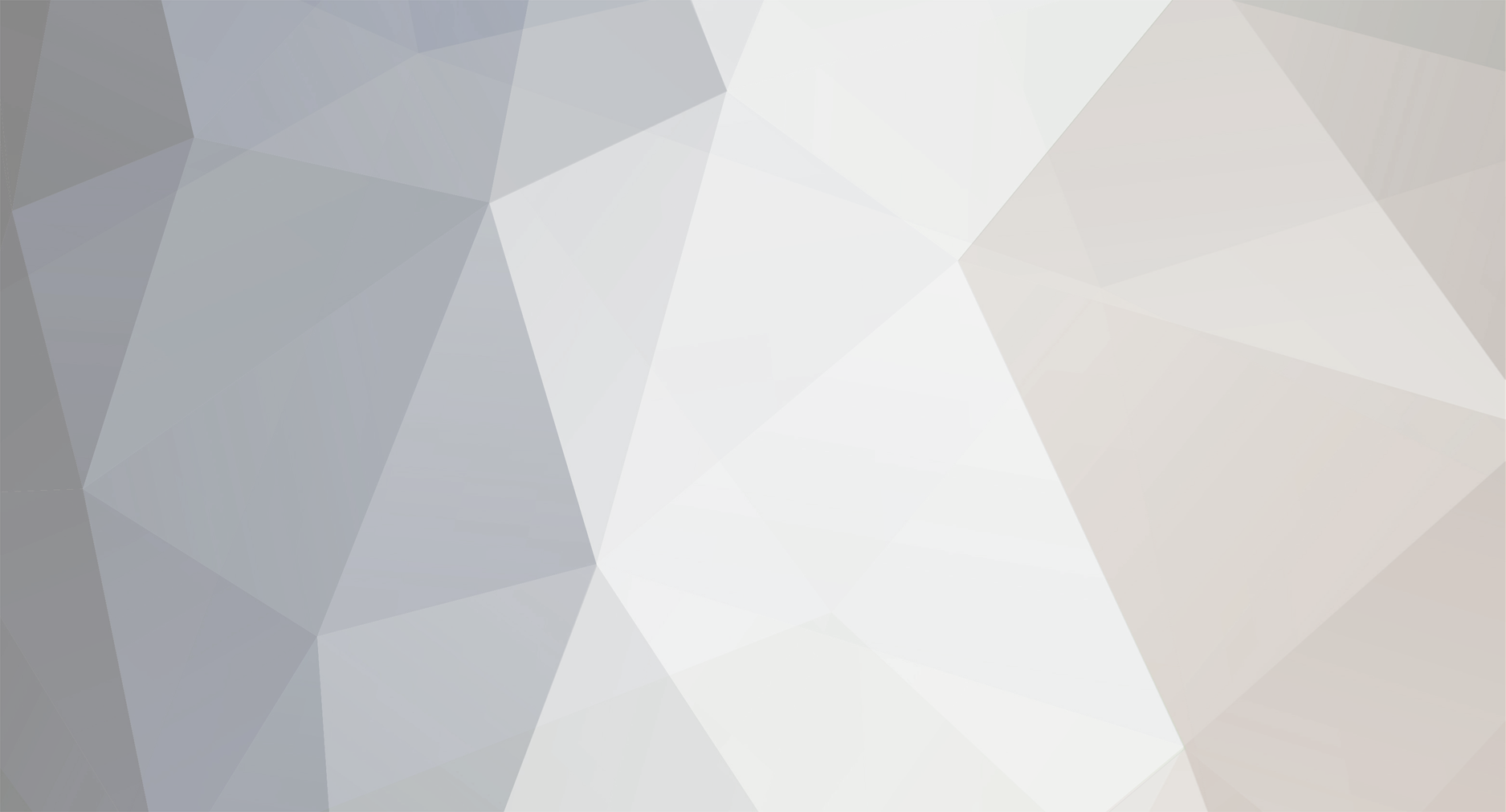
tom kyler_dup1
Member-
Posts
120 -
Joined
-
Last visited
Content Type
Profiles
Forums
Events
Articles
Marionette
Store
Everything posted by tom kyler_dup1
-
That's the wonderful part of vectorscript. If you use the plug-in command to create a new command, add some interface elements, then you can add that to your workspace and it's as good as if VW coded it themselves. It is now a command in VW. Nice work Lamberto! [ 08-25-2004, 01:28 PM: Message edited by: tom kyler ]
-
Here's a screenshot
-
Ziska, a majority of the time, you'll get that message when the line before it (140 in this case) is missing a semi-colon at the end of that line. You might try re-copying it...I know that sounds trivial, but for me, cutting and pasting in VW11 resulted in a correctly compiled script and it ran great.
-
Ziska, You've cut and pasted too much....there's a line in there that says ..."{copy lines below}. You should copy everything below this line and you should be fine.
-
Jean, Plug-ins don't exist in the vectorscript palette. The easiest way to is use the resource palette, just right click (or control-click on mac) and select the second option "New resource on ......" and then select Vectorscript. You can name the palette if you wan't, but I just leave the default name in there. I also leave the default name for the script...the script editor will pop up and you can paste the code in there. Then it will show up in the vectorscript palette. After that, you can just mess with the constants in the first part of the script to size your cone and rectangle.
-
Lamberto, that is a wonderful script, very well executed. I'll post a picture of the results for everybody later in the day. [ 08-23-2004, 09:09 PM: Message edited by: tom kyler ]
-
Lamberto, pictures didn't come through, but defintely interested in that kind of a script.
-
Yes, I have that problem almost everytime I try to use it. If I recall, I even sent a file to Biplab for him to mess with...it was a twisting handrail for a stair...with two end profiles and maybe 3 intermediates. I couldn't get that thing to work. I think that function needs some work, I've seen other posts that relate to controlling the "twist" of a profile as it's extruded and I hope it gets some attention, I seems to use it a lot. And yes that method is convoluted too, that's why I didn't try to model it :-) [ 08-18-2004, 09:52 AM: Message edited by: tom kyler ]
-
Jean, Your problem isn't as much modeling related as it is layout related. The way to model that shape is to create two nurbs curves....one for the top edge of your rectangle and one for the bottom and then loft the two together. Of course the problem lies in creating the 3D nurbs curves. I'm keeping in mind that your trying to maintain a rectangle shape as it wraps around the truncated cone. Unfortunately, a tapered shape doesn't lend itself to a rectangle "spiraling" up the shape very easy, except at low taper angles of the cone and/or high helix angles of the rectangle, but then you run into some other problems. There's two way to attack this in my opinion. (1). Unfold your cone like shown below. There are formulas for this on the web...and then overlay your rectangle. This shows where your rectangle will lie on the truncated cone. I know it looks funny, even an optical illusion, but that is the way it will be. So place your rectangle, then use the grid to determine some offset points. Then in plan view and front view, you can play with the nurbs verticies and "map" them out in polar coordinates....just like plotting in math class. Use the same number of verticies for the top and bottom curve. The other option (2) is quicker and easier and cheaper, and that is to approximate it, fake it, or reduce the taper angle of your tower...the closer you get to a cylinder shape, the easier it is to approximate. If you want to maintain that rectangle shape, then you definitely have a challenging shape to model there. Best of luck. [ 08-17-2004, 11:02 AM: Message edited by: tom kyler ]
-
You've certainly picked a good challenging problem. Here's how I would attack it. The technique I would use it to draw both edges of the ramp with nurbs curves, in 3D, and then connect the two with the loft tool. To ensure the best model, you should try to have the same number of verticies on each nurbs curve and make sure the curves have the same direction...then you should have no problem. The challenge lies in creating the 3D edges, I can't think of a "non-time consuming" way to do that, but you said you have already created a nurbs path. I'll guess it's for one edge only. I would create an equally careful edge for the other edge of the ramp and loft them together. If you have nurbs curves that represent each edge of the ramp and they're placed to your satisfaction, you should have no problem. In addition, you should try to keep vertices on each edge "opposite" from each other and each "opposing" verticies should have the same Z value (assuming you want a ramp whose cross section is parallel with the ground. In the ramp below, I used the shell tool after creating the intitial ramp to give my ramp some thickness, this is optional. Good luck [ 08-14-2004, 11:49 AM: Message edited by: tom kyler ]
-
Removing Solids ... File is Huge
tom kyler_dup1 replied to APE Design Ctr's topic in Solids Modeling
Are these CNC shapes 2-dimensional? ...getting cut out of a sheet of plastic? If so, then I'm guessing you're doing 3D modeling for visualization purposes. If you're doing CNC surfacing of 3D parts, then the above suggestion by Kaare is the way to go, but if you're going to use a CNC for cutting 2D shapes out of a sheet of something, then a 3D model isn't necessary...certainly not cost-effective; however, if a 3D model is what you have to work with, and you need to create 2D shapes to export as DXF for a CAM program and CNC machine, then here's what I suggest: Consequently, the below process basically creates 2D lines from the 3D model. Orient the model in top view, like looking down on a CNC table. Then select all the 3D objects and go to TOOL>CONVERT COPY TO LINES. This will create a group of lines which is a 2D "view" of the screen and keep your 3D model intact underneath. Then grab the group of lines..move them off to the side and ungroup them. You can then cut and paste these lines to a new file to be exported as DXF for a CAM program. There's a few down-sides to this method. but for 2D CNC work, it suffices most of the time. -
When using the offset tool, I would like the new offset line to be deselected so that I can click on a line, then offset....click on a new line, then offset again..and so on.
-
VW "lite" ?
tom kyler_dup1 replied to propstuff's question in Wishlist - Feature and Content Requests
I think that would be a great idea too. I work with some small cabinet shops doing CNC work and they are trying to use these CAD-CAM programs with the worst interface for drawing. I show them Vectorworks and they're astounded at the east of use for 2D line work. Ashlar used to have Drawing Board which would be ideal, but isn't available anymore. I've often wanted a simple 2D, quick launching program to produce 2D parts for CNC work. Small shop CNC is becoming more viable and the low-cost CAM software solutions routinely use DXF for input. I like the idea. -
hidden line renderings not finished in 11
tom kyler_dup1 replied to grantvz's topic in General Discussion
First thing is to make sure those solid objects have a fill in the attributes palette. If not, they'll render as wireframe. -
editing a 2d shape & retaining its dimensions
tom kyler_dup1 replied to mentalenergy's topic in General Discussion
For the example you've given..with a square, there is a preference under the file menu...FILE > PREFERENCES > VECTORWORKS PREFERENCES, under the "edit" tab make sure the box "eight selection handles" is checked. When a square or rectangle is selected with this option on, you'll get "vertex" on the sides of the square or rectange that you can use the re-size the box in that dimension only. For irregularly shaped polygons, you'll have to use the lasso selection or something similar in combination with the shift key to drag in one direction only. -
Searching for best way to make a window schedule
tom kyler_dup1 replied to ekb's topic in Architecture
ekb, Here at our office we keep ridiculously complex schedules that rapidly change and I can tell you of some of our experiences. The only way to go in my opinion it to attach records to your window symbols. Your schedules will be created from these records and that way if the symbol is in the drawings, it will be on the schedule. We use the "link text to record" to generate our on-screen and printed labels next to each symbol. This works by taking a field in the record and writing that data on the screen . This system helps us identify inconsistencies quickly when we generate our report by ensuring that each door or window symbol shows up on the report, even if it's off to the side of the printed page for some reason or duplicated on top of themselves. For every window on the drawing, it will show up in the schedule. So our schedules basically count the door or window symbols in the drawing and write in all the detailed data from the records we have attached to that window or door. It's quick and easy. [ 07-15-2004, 11:26 AM: Message edited by: tom kyler ] -
NOT QUITE SO SIMPLE BEAM CALCULATOR
tom kyler_dup1 replied to CipesDesign's question in Wishlist - Feature and Content Requests
That's exactly right, the beam profile is where the MOI is calculated from. With regards to Ymax, that depends....every Ymax will have an associated maximum stress associated with it. Assuming that the stress at a given Ymax is well within acceptable levels, then the issue isn't the stress anymore, but rather what kind of problems might occur from that kind of deflection. Cracks, or visual deflection might be unsightly and would be undesireable in such cases. As far as 1/2" being excessive, it would depend on the beam, if it was a 2 x 4 beam laid on the flat, then 1/2" ain't bad, but for a 4 x 4 x 8' beam, 1/2" would be pretty bad. In general, I think 1/2" deflection for an 8' span in construction is not very good, and a stiffer beam is called for, either by changing material or changing the configuration or dimensions. What's tricky here is using a proper numerical value for the modulus of elasticity. Solid wood would be different from a gluelam of course, as would a truss. The published numbers are averages and are only a general guide, but are the values commonly used. Common sense goes a long way here, and if a beam supports the load OK, then go with what you feel. If you're the designer and you don't like 1/2" deflection for whatever reason, even gut feelings you can't explain, then go ahead and make a change..you might piss off a few engineering types, but you can't please everybody. As engineers, we're responsbile for making sure designs work and are safe. Anything above and beyond that is up to you, I'm a big fan of maintaining aesthetics and don't mind over-engineer stuff if it looks good. [ 07-14-2004, 02:21 AM: Message edited by: tom kyler ] -
NOT QUITE SO SIMPLE BEAM CALCULATOR
tom kyler_dup1 replied to CipesDesign's question in Wishlist - Feature and Content Requests
Peter, I agree totally that you should be able to do quick, early calculations for sizing beams...so a quick engineering lesson. Fortunately, VW has a command called "engineering properties" in the tools menu that can give you the moment of inertia (MOI) for any shape you can draw. Since sizing a beam generally means specifying the cross sectional shape and dimensions and defining the material (modulus of elasticity value) You can alter the shape of your beams quickly and get the new MOI for the beam calculator. The size and shape of a beam (cross-section)is described by dimensional geometry..web thickness, flange thickness, flange width, overall height, arc radius, whatever, etc....and this dimensional geometry is what is used to calculate the Moment of Intertia of a section, it's calculated with geometry only. Vectorworks can calculate the moment of inertia of any closed polygon and if you want the MOI of a I-beam or something similar, you can look in a table, or use VW structural plug-ins and convert them to groups to calculate their MOI. When you select an object and go to TOOLS>ENGINEERING PROPERTIES, you'll see several values, notably Ixx, and Iyy. Ixx and Iyy are the moments of inertia about the x and y axis that passes through the centroid of the area. Almost all the time, you'll use the Ixx value, because the load (down) is normal to this axis and the beam is bending in this plane...that's a simplification, but it works. If you want to try different sizes, you just change the cross sectional shape (taller or wider, thicker flange or whatever) and recalculate the MOI and put that value into the beam calculator. You can then get the max stress and compare it with allowable values. This is the iterative process for Vectorworks. You can work backwards by specifying the maximum deflection or maximum stress, and figuring out the beam dimensions, but this involves rearranging the equations manually and is probably longer than using the iterative method which is what I do now. Hopefully, you're not thoroughly confused and you can make some sense of it, because a thinking designer is always a pleasure to work with. [ 07-13-2004, 10:55 PM: Message edited by: tom kyler ] -
NOT QUITE SO SIMPLE BEAM CALCULATOR
tom kyler_dup1 replied to CipesDesign's question in Wishlist - Feature and Content Requests
Peter, indeed it is a "simple" beam calculator. For a simple beam to withstand a given allowable stress though, many different variables can be altered to satisfy the stress requirement numerically; however, the software doesn't know which variable you may want to alter and therefore, for most circumstances, it is not be a prudent design method to let the software size the beam, but rather you design the beam and let the beam calculator give you feedback on your design. With a good understanding of beam loading, stress and mechanical properties, sizing beams is not to difficult or time consuming and the beam calculator eases the process greatly. As an engineer, I don't like the idea of architects or designers trying to use Vectorworks to size beams automatically...hence my two cents of input....however, I could see engineering properties working on structural shape plug-ins without having to convert them to polygons. This would make sizing structural elements a bit quicker. Tom Kyler Mechanical Engineer San Antonio, TX [ 07-13-2004, 05:46 PM: Message edited by: tom kyler ] -
In the past, we purchased Pantone color software for macintosh that allowed us to create new color palettes in Vectorworks using the installed Pantone colors. The pantone colors were not specific to Vectorworks, but rather OS X, and Vectorworks is able to use those system colors.
-
Andy, in general that's not a simple thing to do. For simple hatches it could be, but for more complex ones, you would have to calculate new values for each level in the hatch. You mentioned you tried obvious things so I hope I don't insult you, but I'll mention it anyway....The quick solution is to use the Hatch command under the 'Tool' menu and you can specifiy the start point and rotation of any hatch. The down side is the hatch is converted to a group of lines and if you re-size your hatched object, you'd have to delete the hatch and re-apply it using the hatch command again, but that is the quickest way to deal with rotating a hatch. [ 07-12-2004, 06:28 PM: Message edited by: tom kyler ]
-
visible Loci
tom kyler_dup1 replied to propstuff's question in Wishlist - Feature and Content Requests
Nicholas, I've got a work-around if you're interested. It's a script (command plug-in in this case) that brings all the 2D loci to front and makes them red (or whatever color). I put the command in my document context menu so I can access it with my right mouse button (or option-click) and it's a quick work-around fix to get them all visibile quickly. As far as printing loci, I agree that should be an option. -
Anybody notice this beside me. I pick the 3D selection cursor, then grab a handle on the working plane to rotate the working plane (not in-plane with ground plane)...I begin to rotate the working plane, then use the tab key to numerically enter the angle. After numerically entering the angle and hitting "enter" the working plane will set, but then whenever I click another tool..say to begin drawing on it in 3D, the working plane goes back to whatever angle you just tried to rotate it from. I have to click on "look at working plane" to get it to stick. (when using numerical input, not graphical) Here's another one...maybe it's just me. I begin to rotate the working plane in a 3D view....by graphically dragging the handles...as I'm rotating the working plane...I watch the angle in the info bar. Let's say as I'm' dragging the plane...the angle in the info bar says 28.96...and I then tab and numerically type in 30.00. What's happening is the plane is setting opposite the side I want it to. In 2D terms, it's like wanting a line at 45 degrees but having it drawn at 135 instead (cartesian). VW11 on a Mac I notice that as I rotate the working plane, the angle shown in the info bar never goes over 90 degrees. It's more logical to show it going at least to 180, and maybe a negative 0 to 180 also. It would be nice to rotate this with global or relative values. The more developed the 3D power pack becomes, the more I see the working plane needing to adapt also...it's becoming very imporant. [ 07-01-2004, 07:24 AM: Message edited by: tom kyler ]
-
This applies to NURBS surface modeling....and boy are you getting close! I'm loving it! 1. Show points globally preference (interpolation points & control points) When creating surfaces from curves, intersecting curves are important, and being able to snap to the interpolation points on another curve is imperative. Right now, you have to select a curve to see it's interpolation points (and only if you drew a nurbs curve by that method) and then use the cursor hints to snap to that point. Drawing curves using control points are more intuitive, but don't allow you to see interpolation points to snap to when creating curve networks. At this point I usually use the polyline tool and then "convert to nurbs" so that I can see the interpolated and control points...BUT I do not maintain tangency on either side of the interpolated points so when I try to reshape the nurbs curve, I get "sharp" or "broken" points. 2. Lock points to first point (or maintain constant "Z" value into the page in orthographic views) when creating nurbs curves. This pertains to creating planar sections for lofting surfaces (and creating curve networks). Planar sections for lofting are usually created in an orthographic view and in the course of drawing a nurbs curve section, you frequently have occasion to snap to other nurbs curves (if you can see the interpolation points) and right now when you draw in an orthographic view and snap to a curve, then finish creating your curve, the curve usually isn't planar because the points not intersecting the "snapped to" curve are on another plane. Now you could move the working plane to a interpolated point and draw, but if you had to snap to two points on a nurbs curve (for alignment reasons) then even that method wouldn't work. 3. Maintain same number of "points" when offsetting nurbs curves. EXAMPLE: I create a planar nurbs curve with 5 verticies and then use the offset tool. I then get a curve with 22 verticies, making it tough to align "V" curves for creating surfaces. 4. Project curve to surface (and not trim or split) This is more a convenience since it is can have a workaround somewhat. I would like to be able to project a curve onto a surface where the curve doesn't have to extend past the edge of a surface when in an orthographic view, and the cuve is an independent entity after the operation. I know you can project a curve onto a surface where the curve does not extend past the surface edge boundaries in ortho view, but you cannot extract this curve after the operation. 5. Better tesslation control over generic solids (or in general) OK, there's probably not enough of us to justify this one, but here it is anyways. I'm using VW more and more for 3D modeling, but use other applications for animation and rendering....and to keep file sizes down and increase the chances for import success, I create generic solids when I'm ready to export. The 3D conversion res settings usually tesselate too high or not enough. It would be a convenience to have better control over this.
-
Why does does the Fillet Edge tool not work?
tom kyler_dup1 replied to christian's topic in General Discussion
Christian, this topic has indeed been going around a while and I believe the real problem is not Vectorworks, but rather a lack of communication of the particulars of how the fillet tool works. Let's use your windshield wiper example. What if you took your car back to the dealer complaining that the windshield wiper didn't work only to find out that you had to turn two switches simultaneously to get them to come on. Ridiculous I know, but in the above example, the problem wasn't with the wipers, but with the communication of what what involved to get them to work...there was a little more than meets the eye. Vectorworks target market does not have the 3D modeling background of industrial designers, or animators who work extensively with surfaces and filleting, and there's a little more to getting that fillet tool to work than appears on the surface, or is explained in the manual. There are some very particular things that have to happen for the fillet tool to work properly and the way Vectorworks retains the creation history of an object often interferes with getting the fillet tool to work. Sometimes you have to forego the creation history and convert your model to nurbs, ungroup, then "add solids" to be able to fillet entities. So my perspective is this...until a relatively thorough work is written explaining surface-surface interaction, single and dual sided surfaces, edge and face directions, self-intersecting surfaces, etc. then I see much confusion on the part of most users. A simple update won't solve the problem. Before VW came out with the 3D powerpack, I used a surface modeling program that used nurbs extensively and learned the "rules" of modeling there. I've tranfered that knowledge to VW and have had very good success with the fillet tool since. Unfortunately, I can't offer a simple solution because there's a lot to it, but maybe if you're having trouble, you could describe your model and situation and we can figure out what's going wrong. The most common problem I see with the fillet not working is the status of the object as shown in the OIP is not compatible. [ 06-24-2004, 11:02 PM: Message edited by: tom kyler ]