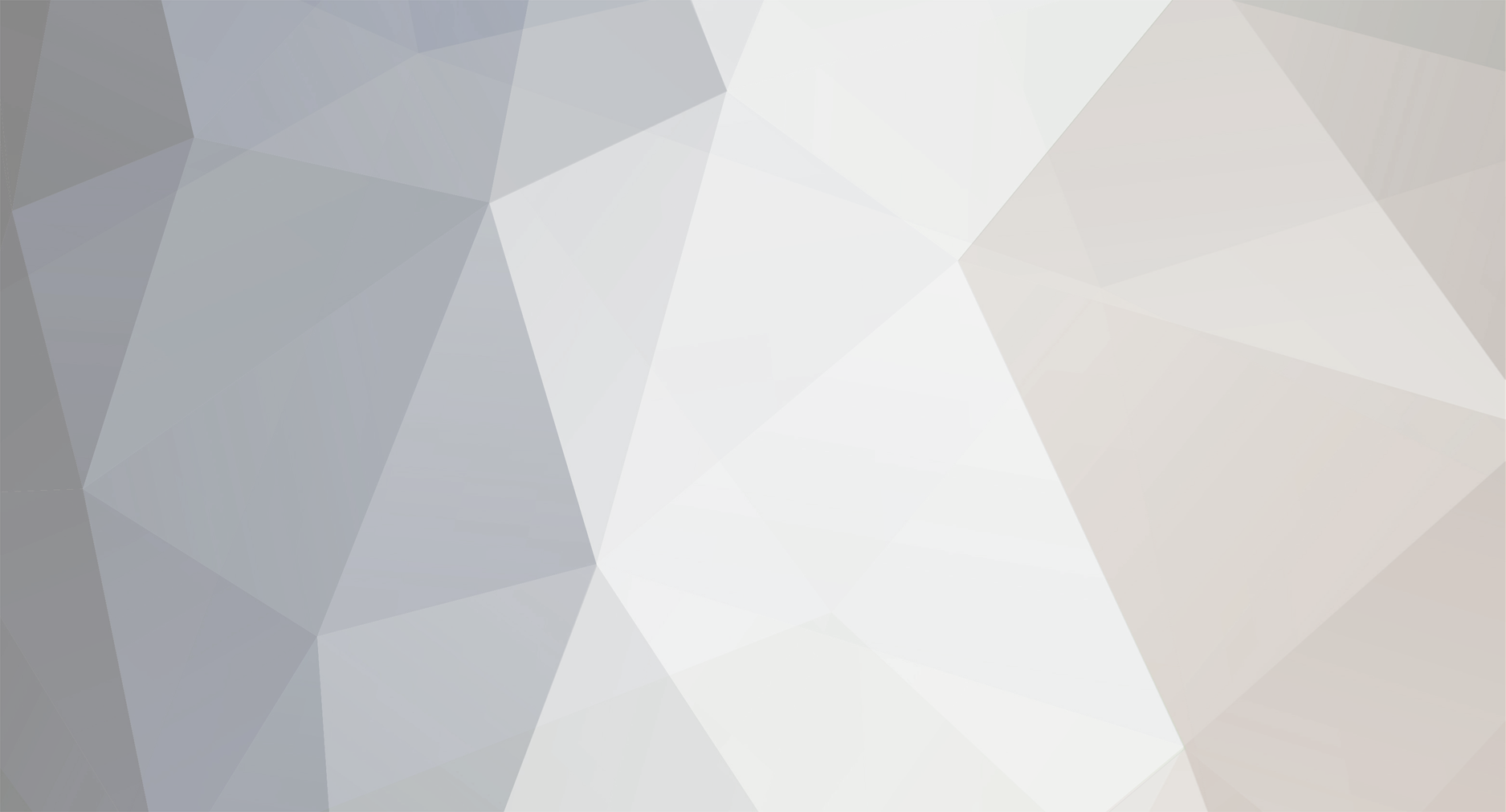
BartH
Member-
Posts
309 -
Joined
-
Last visited
-
Backup Working Files in Project Sharing Workflow Saving as VWX not VWXW
BartH replied to Josh B's question in Troubleshooting
I think I see the issue. In 2024, the Live file could commit changes to the Project file, while the Backup still had those items checked out. Trying to perform a Commit/Refresh in the Backup file caused a conflict with the objects that are both checked out and committed, right? Like "Schrodinger's Commits" To solve for that in VW 2025, you removed the functionality of Backups being connected to the project file. But we already have tools to capture conflicts. I sometimes see a message saying: "USER B has updated this Viewport Style. Do you want to use their version or yours?" Hopefully, there is a way to build in some conflict checks and restore the ability to commit from a Backup after a crash. I appreciate the hard work and problem-solving. -
Backup Working Files in Project Sharing Workflow Saving as VWX not VWXW
BartH replied to Josh B's question in Troubleshooting
I think I see the reasoning. However, in my working model, backups are for crashes, and version control is for managing unwanted changes. Maybe I'm using backups wrong. VW still does crash - not a ton, but when it happens, it hurts. If I am working on an edit that I might need to discard or undo, I'll create a new layer (object A version 2) and work on it there before getting rid of anything. Say I've got a Project_Mine.vwwx file that has items checked out, and suddenly VW crashes. In the new process, I have to open the Backup, and manually audit it for every change that didn't get saved since my last known save, whenever that was, and one by one copy/paste objects, re-do class changes, copy or rebuild tables, textures, everything, one by one. It is a far more cumbersome process. Before, the Project_mine_backup.vwwx had the snapshot and all of the process to create that snapshot intact, including all the objects I checked out. If I opened the Project_mine_backup.vwwx, do a save and commit, then recreate my Project_mine.vwwx file, I am back up and running with minimal losses. So following your language, in the event of a crash, I would much rather recover work from a backup and have the backup throw away the live file. Because I can rebuild the live file from the Project file, once my edits are committed from a backup. It is far less likely (for me) that I do a save and commit in my live working file, keep working for some time, and then realize I don't want to do that commit. In that case, I would go back to a "dead" backup and copy/paste changes to the live file. At a minimum, there should have been a bulletin that said, " Hey, we changed how project working file backups work; you can no longer commit changes from a working file backup. DO NOT rely on backups to be connected to the project file." -
Short answer, yes. But it all depends on your expectations. dive in deeper here
-
Backup Working Files in Project Sharing Workflow Saving as VWX not VWXW
BartH replied to Josh B's question in Troubleshooting
I wonder if @dpicolo or someone from the VW team can clarify if this is a feature or a bug? -
Hi Sorina, My travel machine is an Asus TUF F15. a similar model from 2022 with the RTX 3070 GPU I run VW well enough with some fairly complex models. The GPU in your ROG is a full version newer than mine and about as fast as they get. For working in 3D shaded mode, you will be in great shape Rendering is as complex as you want to make it. And speed depends as much on which rendering engine you use and on your desired settings. For a laptop, you will have excellent performance, but if Rendering is a priority, one might consider a desktop PC with TONS of RAM, or Cloud Rendering. Bart
-
Backup Working Files in Project Sharing Workflow Saving as VWX not VWXW
BartH replied to Josh B's question in Troubleshooting
I've seen this too. I was really frustrated after a crash. I used to use the same technique to commit from a backup working file, But the backups are no longer Working files connected to the project. -
How do I make the post stop against the top rail?
BartH replied to Ramon PG's question in Troubleshooting
Make the Guardrail Height the same as the Handrail Height - 1/2 the Top Rail Depth to have it "miter" with the top rail. Or, Guardrail Height-Top Rail Depth to have it Butt against the bottom of the Top Rail. . -
Help with Working Planes and Rotation tool
BartH replied to Cristiano Alves's topic in General Discussion
Got it, Are these by chance Spotlight Symbols? The action you are looking for is absolutely the default. I believe the only way they rotate about their individual origins is if they are Spotlight symbols which are intended to function differently. depending on how the symbol was built. But I am not a spotlight user so I can't say much more. Maybe @Jesse Cogswell can "illuminate" the conversation. -
As @Gaius said, Learn to use Numpad 5 and Numpad 0, to flip back and forth between Top/Plan (unfilled 3d objects*) and Top ( filled 3d Objects*) *assuming shaded mode
-
Why not ask Grok? I hear the creators know a thing or two about space.
-
Help with Working Planes and Rotation tool
BartH replied to Cristiano Alves's topic in General Discussion
Hi Cristiano, There are a lot of good tutorials on Youtube RE: Working planes: https://www.youtube.com/results?search_query=vectorworks+working+planes It is hard to tell what you are trying to do in your rotate example. A rectangle might be a better demo object to rotate so we can see what your desired outcome is. What is the object you are trying to rotate? A hybrid symbol might not behave as expected. -
VW will download a resource automatically if you drag it into your file in the RM, or into the working view. You might have to Refresh the Resource Manger folder before newly added assets show up.
-
You can look at the Settings in the viewer. Generally the render quality is "optimized" for generic users - think of people on laptops without good graphics cards. But you can turn on Ambient Occlusion or change the Lighting from "Sun and Sky " to "user view" for interiors. I have found that a Tablet / iPad with the VW NOMAD App does seem to have better lighting capabilities. So If you client can install the NOMAD App you could " Use Scene Lighting" as an option. Lastly, you could try using the VectorWorks Presentation and set up a series of linked panoramas, These panoramas can be hi-res renderings. if image quality is more important than a true walkthrough. Bart
-
Have you tried a VGX file ( formerly "WebView") ( this may only work with Vectorworks Cloud Services) Export as VGX ( 3D only) Save to VW Cloud. Get the sharing link and send that to you client. Bart
-
Hello @CBST Welcome to Vectorworks. We design Museum exhibits so we might be in a similar use case. I am sorry to say that I don't know of a lot of specifically SketchUp to VW tutorials. If you have found VW University, you are off to a good start. Your best bet might be to throw some examples up here of what you are looking for and the Forum will likely jump in to help There are a few YouTube channels worth looking at too. Some are more Architecture focused but still very helpful. https://www.youtube.com/@archoncad - Jonathan Pickup https://www.youtube.com/@jonathanreevescad https://www.youtube.com/@austinvectorworkscommunity Bart