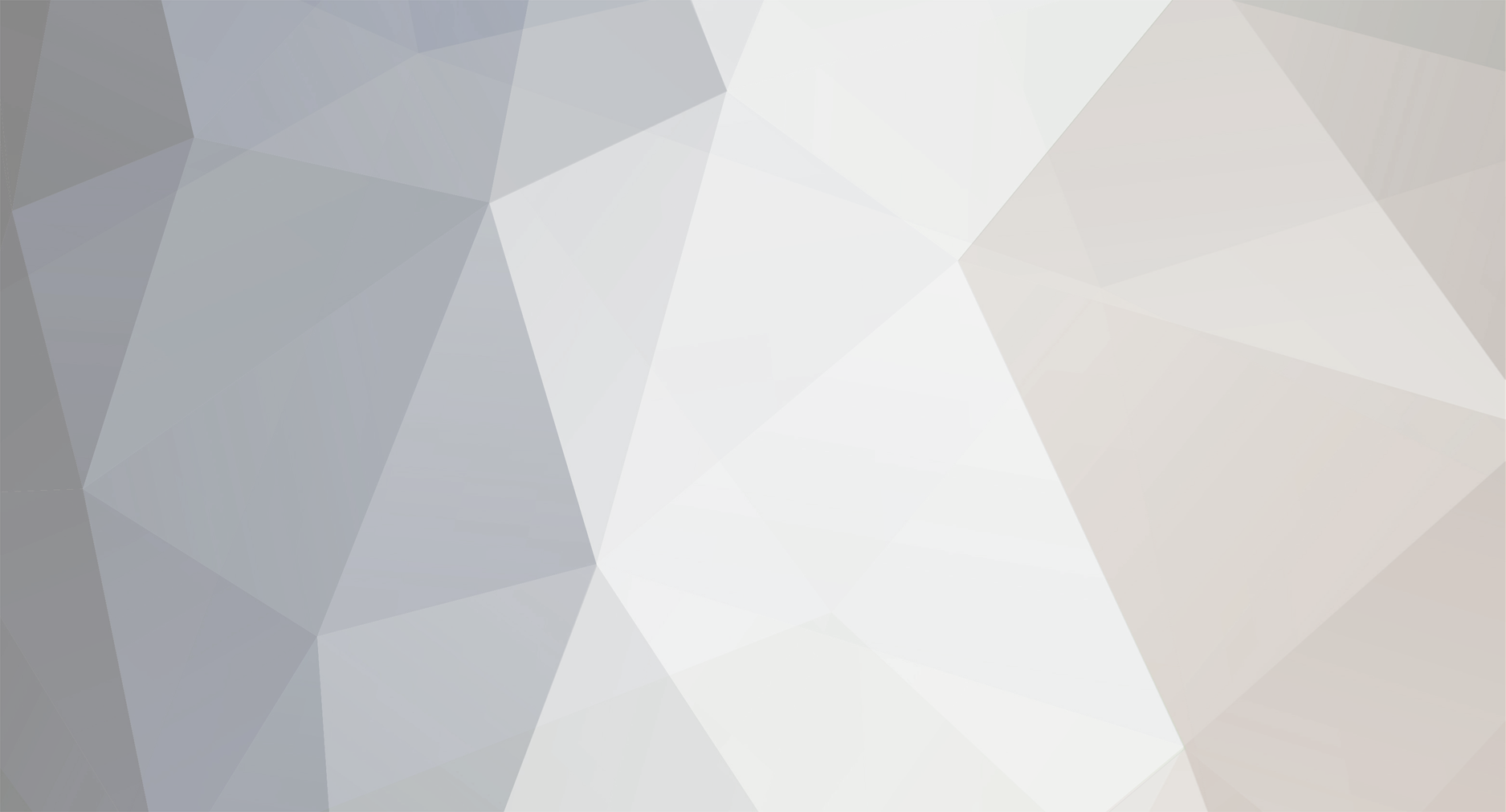
Thomas_
Member-
Posts
47 -
Joined
-
Last visited
Content Type
Profiles
Forums
Events
Articles
Marionette
Store
Everything posted by Thomas_
-
So I have some Meyer MM4-XP cabinets with EN3 5-Pin inputs. These are a pain to utilize, so in general I make EN3 to 5 Pin XLR adapters when working with these. I went to draw these in vectorworks using the adapter, but it seems the adapters are only designed to go on the right hand side of equipment or outputs. I inserted an adapter, edited and mirrored it manually, but the moment I connected it to the input of the MM4, it flipped orientation automatically and as a result appeared over the symbol for the MM4. Am I missing something or ddo these not work like I would like yet?
-
I will say there is possibility to this due to ethernet especially. If you start documenting Network switches, and show protocols being transferred over (As well as VLANs etc.), I could see this being useful, but not quite as simple as one might like. Would take a bit of work to get correct. Thomas
-
Vectorworks abandoning perpetual licences
Thomas_ replied to line-weight's topic in General Discussion
See my first post here, this is my world and I just don't see that being the case, some of them were already offput by the handling of COVID, many of us work with tight incomes so many people wouldn't upgrade every year as a result, often doing anywhere between 3-5 year cycles because of price. -
Vectorworks abandoning perpetual licences
Thomas_ replied to line-weight's topic in General Discussion
And by the way, would have had me most likely start paying for a second license right then, instead of determining if I need to invest that money elsewhere, so likely to result in MORE income for the product, instead of potentially less. I probably still would have kept my perpetual license and SS in place of course, but this would be easier for me to justify purchasing an additional license for my employees than the current state of things. Yes it feels weird sometimes to realize that charging less can lead to more revenue, but at the smaller end of the scale, in this case it very well might IMO. -
Vectorworks abandoning perpetual licences
Thomas_ replied to line-weight's topic in General Discussion
So here is my thing, as a small business owner: I currently own one license, and am a service select member at $800 approx a year. This is not a small price, nor was the initial cost of the perpetual license, for me to absorb. It does at least mean that if I ever stop paying I can continue to utilize the existing version. If I was to purchase a second license, which I have been looking at for some time, my annual cost will jump from a one time fee, which I can absorb with a couple of larger jobs, with $800/yr, to $2200+/yr on a monthly license which as a business owner is easier to handle sometimes. That one time fee is $4500 (Spotlight+ConnectCAD) so looking at the difference, in about 3 years this will be costing me an additional $1200/yr to operate a second license, that if I do ever cease payments on, I will lose all access to, instead of just sticking with the current version. I just can't see how that in any way benefits the end user on the small scale certainly. For the larger global business I am also part of that i am considering pitching Vectorworks for, it may not make a huge difference to them, but for the small business it is huge. This is also true for the freelance entertainment professional, many of whom that I work with tend to upgrade licenses when they can afford to, but can't afford to all the time. This is REALLY going to screw them over, just as that industry is starting to recover from being shut down from COVID for such a long period of time, and may drive an entire industry away in my opinion. Personally I hate where industries are going to this model, it is horrible for the end user. This now has me considering instead of purchasing a second license and a second subscription for service select, whether I should instead invest that money into other products, many of which are cheaper than vectorworks to the point of being able to afford multiple just for the difference in cost, much less to say the total investment. -
Thank you glad to hear it! This is still good knowledge for me to have though as I do want to learn my way through the vectorworks api to understand the scripting capabilities a bit more though. I would still encourage making everything available via API as much as possible for things, for instance right now I am working on setting up a streamdeck profile with my most commonly used tools, and finding the lack of bindings a bit troublesome for this, but if I could call from an API I might be able to create a single plugin that would allow me to use two key combination bindings (ala emacs, or qcad if you are familiar with that) to expand the available bindings, and allow me to more easily set up those shortcuts possibly by using multi-actions on the streamdeck to emulate the keybindings. All that being said, being able to click once to create a socket that is a Mic input with XLR-F connector on the left hand side (Or an array of them) would go a long way to helping to speed up creating new devices so I look forward to seeing that.
-
So finally had a moment to look at this while a show is loading out. These is a SetToolwithMode function that seems like it might be related (But maybe not exactly what I want), but I can't tell how to determine the INDEX of the SocketTool (Or the groups, etc. but will get to that after I get the selection working). I did test SetToolWithIndex('SocketTool') and despite returning '1' (aka TRUE) as the bool, it definitely did not select the tool, and I suspect this is a bug that might need to be looked at at some point (The fact it returns TRUE even if it can't actually select the tool that is). SetToolWithName('SocketTool') obviously does work, but SetToolWithMode requires an Index, and I just can't figure out how to determine the index of the ConnectCad tools as they are not listed in the appendix with the rest of the tools. EDIT: I have been trying to utilize vs.ws2 functions to try to get the tool index, but am having problems with tool paths. Based off my reading of the API, I would be able to, for instance: vs.Message(vs.ws2GetToolsCnt('Tool Sets/Schematics')) But that returns 0 which should be the count of tools in that tool set, so obviously I am doing something wrong there. Any hints? If I can understand how to correctly address the tool path, I should (at least in my head) be able to then utilize vs.ws2FindToolIndex() to find the index (Assuming I can figure out what is meant by 'Universal Name' in that function. That in turn would give me the indexes I might be able to pass to the SetToolWithMode command supposedly?
-
Thank you, will take a look.
-
Which video are you referring to for 'Nikko's Video'? Ill take a look at using custom records for this, though I will say that if this can be more integrated it would be useful functionality in 'Check Drawings' as well. This is becoming more and more common in the AV world as well as IT to have things PoE as more small devices are coming out that can be so would be useful in the future.
-
Thank you, will do so.
-
Answers that, look forward to seeing this working more smoothly in the future as it definitely would have simplified my last set of drawings I was working on tremendously.
-
sockets not connecting AND text still disappears in devices when editing
Thomas_ replied to cessnaflyer's topic in ConnectCAD
So I have had intermittent similar problems, it is not tied to a file for instance, it just happens. One thing I have noticed is that in one occurrence, can't say this for all occurrences, but in one occurrence i was in multi-connect and going to single connect mode made a difference. That being said the problems of the OP still exist for me as well, but wanted to share this just in case it helped anyone else save them from restarting the software on occasion. -
Am I missing something or is there no way to specify manufacturer and model on equipment racks? For instance I am currently designing a medium sized IT install, and want to specify the racks to be ordered, but it doesn't look like I can spec the make/model on the rack itself. I can always do so manually, just wondering if I missed something and if I did adding a feature request. Thanks
-
Another case where this could come into play, when I have a CTP connected to a network switch on either side of the switch (Bi-Directional ports mean L->R reading isn't quite as critical IMO though obviously there is that argument). Again flip Horizontal flips the direction of the arrow and only the arrow, which is great, but doesn't change how the connector itself acts (Coming in from the left side of a red arrow no matter which way it faces will always give a '---' on the cable for the connector)
-
So I discovered Flip Horizontal on devices in ConnectCAD recently which could be incredibly useful in certain situations to save time on relaying out bidirectional ports on Network devices for instance, however it seems to have an issue (Possibly it wasn't intended to be used like this?) So if I have a simple device symbol in the schematic, USB-C on the left, Ethernet on the right. I right click and tell it to flip horizontal as I need the Ethernet on the left to clean up my drawing, the text for those ports does indeed flip correctly and display correctly. However when I connect a cable to what is now the Ethernet on the Left, the cable reads that it is patched to a USB-C port when connected to that device. Obviously not ideal. Similarly, but possibly less of an issue, is that when double clicking to edit the symbol, it now goes back to the original symbol definition (Which is understandable, though would be nice to edit it as is I suspect, so maybe the flip operation should create a new symbol _flipped or something similar?) So am I used this in a way that shouldn't work and wasn't intended, or is this a bug?
-
Is it possible to attach power info to an RJ45 socket on a PoE Switch? This could be useful for several reasons: 1. If a device needs power and is connected to a non PoE port, an error could be thrown in checks 2. If the device power draw is greater than supplied by the PoE port, an error could be thrown Even fancier would be to add a checkbox to devices that are powered over PoE for 'Locally Powered' where it wouldn't throw such an error in checks. Thomas
-
Sadly already have a final system checkout and commissioning scheduled for this morning, otherwise it would be a interesting conversation I am sure. Maybe next time.
-
I am definitely looking into it. It is just a matter of how much free time I have to really jump in, considering that along with my consulting business I am also a production manager for a fairly large road house now as well, time tends to be minimal, but there are enough things like this that would make a significant difference in my workflow that it is worth that time. My background includes programming in C/C++ and Python in the past as needed so obviously Python scripting peaks my interest at least. Thanks, I will dig into the function definition documentation in the next day or two then and see what I can find.
-
Heh sorry I forgot I had mentioned this in the other thread, will carry my response here. Reply to your post from other thread about this: In the meantime, I have been diving into the Python docs to try to find a way to implement this via python, any pointers on where to start (For instance I was expecting a function call to activate a tool, and be able to define parameters of it, but haven't found anything for Connectcad tools (Sockets, etc.) yet)?
-
To be fair, there is a fair amount I disagree with Conrad's approach on some things, but his logic here is sound in my experience (In terms of why it makes sense that every instance of a device is not a symbol that would be tied to every other instance) as all of these are perfectly valid things that I have done repeatedly. Now whether this is an argument about making each device an instance of a unique symbol vs a plugin, eh that I can't weigh in on. Very possible, as has been obvious in other places, very often you and I have very different ideas on workflow It is likely the being forced to shuffle things around that caused me to miss this, as, for instance, when I started I immediately went to the device builder to start building devices. Then to edit those devices, you have to enter the device to move things around, as a result I completely missed this functionality apparently as it is the only interaction that can happen from outside of the device editor. I would be surprised if I was the only one to miss it given this though as I suspect many people probably follow a similar path in their exploration of ConnectCad. So then what would it take to be able to manipulate more about sockets in a similar fashion to what I described above from outside the device editor? As mentioned, since when entering the device editor it changes your view so that you lose your place in the overall drawing, so if trying to align sockets to a device next to it, you need to enter the editor and then zoom back out so you can see it, repeat step one for each device. It would speed that entire process up tremendously, though I am guessing is not a small amount of work as that is a fundamental change in workflow/operation.
-
Ok this is possibly a more generic Vectorworks question, but the use point for me is strictly related to connectcad. Is there a way to take, for instance the socket tool, and replicate it, but with specific values already filled in? For instance to identify a line level audio XLR input on the left hand side of the equipment. That way I could create a tool palette of the most used connectors to build devices with quickly, with a single click instead of 5 clicks and three typed in fields (Exaggerating only slightly honestly). In my systems 90+% of connectors, if not 95% or 99% are really just a handful of configurations that I would like to reuse repeatedly and quickly to build equipment items.
-
Ahha I am coming back into things here doing my every couple month of checking in on the forums and see this.... So put me in as a raised hand of those that would appreciate a switch to remove the 'defaults' as I find many of them useless for me as I recreate them to be more precise in many cases. Difficult? Not really though when you find you need a connector not in the list for new device you don't normally work with, that could be easier. Tedious? Very. I will preface this with, I understand the difference between what i am about to discuss and the amount of information tracked in VW/CC so please keep that in mind, this is just a demonstration. Some time ago I started creating basic tools to do signal flows in diagrams.net (Was draw.io). The basics were, you created a device by drawing the rectangle, and dragged in the connectors to make IO connectors, and if the connector was within the bounds of the device, it would be added to the device, so that if you drug that device, it would drag all connectors, etc. much like you would expect. I have a basic training video and documentation if it would help on this to demonstrate I can send (That I do send to students in fact because it doesn't require them to know VW to make basic diagrams). The difference in speed building a piece of equipment there is tremendous. I don't have to create the device, then edit the symbol, then create each port, then edit each port, the leave the symbol/realize I need to reexpand the device, so edit the symbol again to guesstimate how big my device needs to be, etc. I just created the device, drug in the sockets onto the device, and could select each socket and edit the name etc. individually. Taking that one step farther via things like the eyedropper in VW would make it even easier, being able to apply 'standard' settings, such as Line Level XLR connectors, Mic Level XLR connectors, etc. but being able to drag and drop them directly onto the drawing rather than having to edit the symbol first and having that disconnect between the symbol and what it encompasses and the rest of the drawing that makes layout more difficult. Not to mention the ability to save equipment as symbols and manage them easily does wonders as well to save time in the future for standard equipment obviously. Obviously there is a lot more information in VW, but dang if I kind of dread building the signal flows to start with because I wish it could be much quicker than it is.
-
Can you give an example of the data viz solution you mention? Obviously I have brought up this before of being able to hide sockets, so very curious on this. Thanks! Thomas Vecchione
-
Having done at least a decent bit of programming over my life, I am fully aware. Correct it might not necessarily be easier, but will it really be harder? If not and one option allows for more workflows and options then that would seem to be the better path forward. In this case the differentiation between a term panel and connector panel is odd to me when in the real world no such distinction is ever made that I am aware of, it is just a panel and if I tell an installer that they understand what I mean based off the connector loading. I could be the only one, and just have never experienced this in my dealings and everyone else makes such a distinction, but it would surprise me if so. From a software standpoint it would seem to be determined primarily by the connector loaded as well. And that may work great for you. However I will point out a couple of things: 1. In theater (The world I came from and still teach in, though I also do system consulting as well for installation) I should be able to hand this off to a worker and have them replicate exactly my design. It should be very exact in fact as if it isn't things get missed on the shop order. That isn't to say it will ever be perfect, but the more complete, legible, and precise it is the easier time everyone has. And it means that the crew running the show are more able to follow my paperwork in troubleshooting and if they were involved in the build they know it that much better and can just reference it when needed. 2. As a system designer (Installation or Entertainment) I often use the documentation to double check my work, and often will catch problems or missing equipment because I am this precise. That means less wasted time on site building or waiting for parts to come in. 3. My installers generally don't shut off their brain, if they do I tend to not use that contractor again. Very rarely do I run across that, but they do often appreciate how thorough my designs are (Recently had some confirm this in front of a client) as it means they have to worry less about catching issues, and just need to follow the instructions, and if they do have questions they give me a call as needed, but often times know me well enough to understand where I am going in those occasions and haven't shut off their brains so that I rarely have an issue. Thomas Vecchione
-
Yes but that isn't really what I was asking, what I was looking for was having both a passthrough, and a term connection on a single panel? For instance one example was a small AV rack I put into a gym for a client where I had soldered XLR and a pass-through HDMI connector (Along with various RCA, etc.) for them to plug in either an external system or video presentations etc. Specifically how to show those connectors on a single panel in the rack elevations especially. Thomas