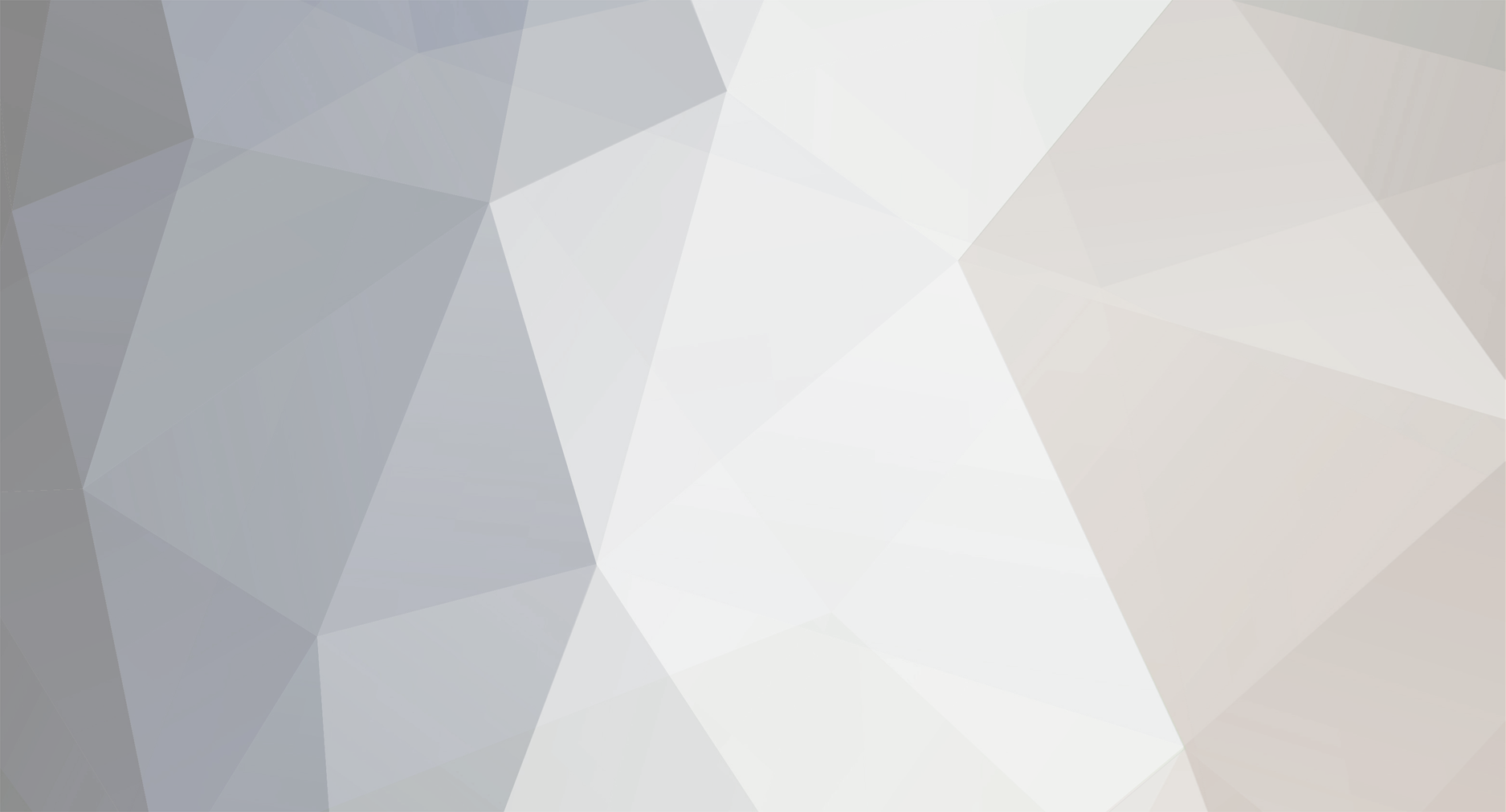
LarryO
Member-
Posts
428 -
Joined
-
Last visited
Reputation
91 ExcellentPersonal Information
-
Location
Victoria BC Canada
Recent Profile Visitors
The recent visitors block is disabled and is not being shown to other users.
-
VWX 2013 - slow graphics and crashing - memory leak
LarryO replied to rozeman architects's question in Troubleshooting
It is not generally the quantity of viewports but the complexity of what they are attempting to render. Then the quantity will multiply the memory use. -
I am finding that when creating a new callout where the leader extends off to the right that the tool creates an instance where the Horizontal Position gets set to "Left" even though the preference was set to create them as "Auto". While this is not immediately an inconvenience, when one is flipping notes for symmetrical reuse it becomes a frustrating !surprise! This only seems to occur in 3 point mode, VW2023 & VW2024. Is this a bug or something I am missing?
-
VWX 2013 - slow graphics and crashing - memory leak
LarryO replied to rozeman architects's question in Troubleshooting
If you have a memory intensive object, or a few of them, (such as an imported pdf object rendered in a viewport, etc.) as you edit them the number of undo steps you are saving can increase memory usage quickly. But this should plateau as you get to the max step saved and only the system swapping memory blocks to disk should slow it after that. Saving and reverting to saved may help but you do lose the undo steps in the process. If that doesn't produce a reduction then is not this specific memory hog. Without context the issue(s) you are experiencing cannot really be diagnosed. -
A mask seems to cover the original line but it extends both before and after the bridge segment and a cover weight of 1 doesn't mask the original line. The original line should be connecting to the bridge segment on each end of the bridge should it not?
-
When editing callouts, specifically addition and deletion of leaders, the functionality missing is the use of ALT to select another callout instance to continue editing. There is a behaviour continuity issue here when compared to other editing operations. One must stop the operation by pressing X before selection of another callout can occur and then reinitiate the operation (additions or deletions). An almost daily frustration.
-
I'm assuming the objects imported are contained within a symbol definition with an instance present on the layer that was create by the import. Here is a scenario to test to see if you are looking at the symbol's plane or the layer's plane when editing. Set the origin of an instance of the symbol to zero,zero,zero (x,y,z) in the IO palette. Set the view of the layer to top or top/plan. Choose to edit the symbol in place and if the symbol was defined on a plane other than the layer plane there will be arrows indicating the direction of the axis. And if you press zero on the keypad twice the view will rotate away from the layer's plan as it switches to the top/plan view of the symbol's defined plane. At which point you can press 2 to get the front view relative to the symbol's x-y plane. Now whether Move 3D Selection responds to the layer's plane or the symbol's plane will depend upon if one selects Cartesian or Working plane in "Move 3D Selection" dialog. At least that is how it generally responds when I use it.
-
Snapping stops working when editing deeply nested objects.
LarryO replied to Bruce Kieffer's question in Troubleshooting
The only reprieve I have had from this issue and it doesn't always work is to change to wire frame. It is like forcing an update in a viewport when trying to dimension in hidden mode and the snaps stop appearing. -
I noticed some unexpected behaviour today while flipping objects within a 3d symbol. VW2023 If I flipped 3d object(s), not grouped, they flipped about their collective middle/centre. If I flipped 2d rectangle(s) on a 3d plane they flipped about the symbol origin when flipped horizontally. The were placed on the x-y plane at z=0 and not grouped, but I don't think it mattered other than that they were not screen aligned. Finally if I flipped those same 3d objects and any one of the 2d rectangles, all of them flipped about the symbol's origin and not their collective middle/centre. Larry
-
Depending upon how you approached the rotation the objects may have already been on the z-axis of the x-y plane of the symbol and it was the symbol that had been rotated 90° in the drawing environment along either the x or y-axis which would have aligned the z-axis of the symbol's x-y plane onto either the y or x-axis respectively of the layer.
-
I have tried a couple of times to use this object/tool because it seems to have a lot of the capabilities one would want for creating and documenting a 3d framing system, but there always seems to be glitches that have yet to be addressed. Like this one in the image. I drew the beam from right to left in plan view before adding the pitch, bevels and miters. I then attempted to rotate it into position but one must first change the view to top/plan because it is recognized as a hybrid symbol and will not rotate in any other view. Then enter the rotation value in the dialog but the rendered view shows doesn't change so I rotate it back to the original orientation along the x-axis. The result is this image. One step behind my action; very frustrating. There doesn't seem to be a setting to keep the end points aligned to the visual object, particularly when there is an elevation change. For the x/y/z-values only the start point data can be reviewed in the object info. VW2024 Views are plan, front and iso in that order.
-
I wonder if this is a result of a change to an event handling or event generating routine, possibly at the system level. I noticed that while using VW2023 there are unpredictable crashes to desktop when clicking the layers button (not the pull-down but the primary layers submenu window). Also bringing up the symbol window when replacing a symbol the button within the dialog hesitates its response until you attempt to move the mouse away from the button, leaving you with an unstable feeling that the program is having a mini-stroke. There are two others I have noticed as well that cause the program to crash to desk top more frequently than past versions, and some of that might be a result of me investing more time into utilizing 3d objects so I wasn't exposed to glitches that could be a result of memory problems from 3d sub-routines. I've actually had those annoying improper call or missing (resource?) something or rather dialog pop up a few times this week. The one that repeats itself 10 times or so before either stopping or crashing.
-
This is VW2024 update 2 (just installed) first launch. Full screen. the shadow line occasionally is shows correctly (as seen in 2nd image), but as soon as VW is the active app it reverts to the image above. Intel(R) Xeon(R) W-2123 CPU @ 3.60GHz 3.60 GHz RAM: 16.0 GB (15.7 GB usable) Product ID: 00391-70000-00000-AA565 64-bit operating system, x64-based processor No pen or touch input is available for this display Windows 11 Pro for Workstations Version: 22H2 Date: 2023-04-14 Build: 22621.2715 Windows Feature Experience Pack 1000.22677.1000.0 <EDIT: why is this version, VW2024 using about 7x the RAM as VW2023 without there being an open file?>
-
Snap to 3d locus for dragging Viewport into position??
LarryO replied to LarryO's question in Troubleshooting
hmmm, this works sometimes but not all the time. Today VW got its cuppa caffeine; yesterday it was not very snappy. -
Should I be able to snap to a 3d locus when attempting to drag a viewport to a new location? What about a symbol's insertion point? Referring to objects in the VP's design layer not it's annotation environment. I know mid, end and a few others are normal grab points, but they are defined by an object like a line or extrusion and not objects in themselves.
-
Why has it been so difficult to stop these lines from occurring? Over the years of VW development no repeatable technique nor application fix has emerged to ensure a predictable outcome for this problem. Aside from tedious masking techniques which require repeatedly scanning viewports after adjustments to 3d objects. This is a simple Wide Flange beam with subtract solids performed to create the round holes shown and remove a portion (cope) of the top flange. Doesn't matter if the subtraction extrudes have three circles or one or if all the subtractions are separate operations or conducted as a single one in this instance.