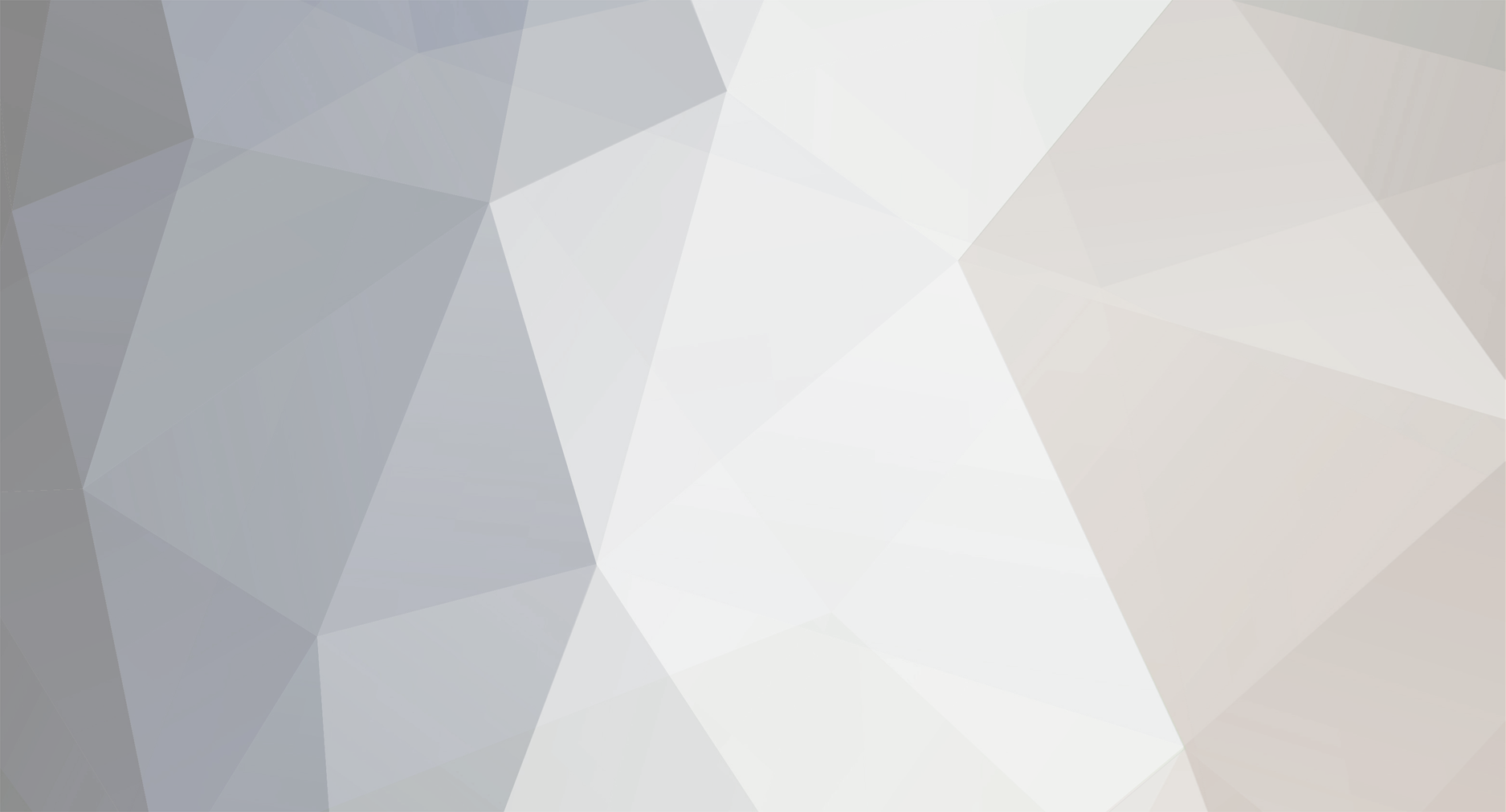
Claes Lundstrom
-
Posts
228 -
Joined
-
Last visited
Content Type
Profiles
Forums
Events
Articles
Marionette
Store
Posts posted by Claes Lundstrom
-
-
I actually use a combination of Renderworks, Artlantis and Keyshot.
Renderworks biggest advantage is that it's inside VW, so there is no need for conversion. It's well adopted for architectural work with lot's of textures, symbols and resources in that area. Applying textures and getting it right can sometimes be a bit time consuming to get to an acceptable rendering quality, as it lacks a separate rendering window with controllable size and an efficient realtime preview features like the other programs have. Texture mapping can sometimes be a bit frustrating, especially if you mostly work with complex shapes like I do.
Artlantis biggest advantage is that it's comparatively straight forward and easy to use once you get the model imported, and provided that the model is well organized. You get from A to B quickly. I have a comparatively old version, and the rendering quality is perhaps not absolutely top notch but not bad either, and since the realtime rendering gives you quick feedback, it often delivers better result than Renderworks based on the often limited time you have to spend on renderings. Exporting from VW to Atlantis can be done through a plug-in, or using .3DS, OBJ, Collada, etc, which works comparatively well.
Keyshot also supplies realtime previews, which are probably better in quality than the other two, by a long way. Importing works well using a wide range of formats, such as 3DS, OBJ, STL, VRLM, STEP, IGES, DXF/DWG, though a major drawback is it's inability to add and correct normals, which is a huge problem from VW as normals is a bit of a mess in VW. Normals, which is used to create smoothing in renderings (draw a sphere, convert it into a mesh and render in OpenGL and it looks edgy despite being set to smooth), is basically not working as it should for mesh models, and that is also carried through to polygon mesh based model formats such as 3DS, OBJ, etc. Keyshot is very strong in textures, but it feels more oriented towards product visualizations rather than architectural visualizations, so it may not be an option for all VW users.
-
4
-
-
Hi,
We are looking for a freelance with VW skills, preferably in the Birmingham - Wolverhampton area. The work involves modification and production adjustments of exciting drawings for a product line of super realistic product physical 3D replicas. If you are interested, please contact me for further information at info@touchcad.com
/Claes Lundstrom
Lundstrom Design
-
I use both, as both have their virtues.
-
-
Point clouds are useful in many cases, but not always. Besides using point clouds, would it therefore also be possible to just extract user defined points, like you can do with for example PhotoModeler? I have done quite a lot of boat cover designs in the past, where we are essentially only interested in the panel edges, getting them as precise as possible, and then re-skin the model manually. In such a case you only need say 100 points or less. The rest of the cloud (99.9999%) is then basically waste info, and usually doesn't match the exact key points used for skinning.
-
Windows only it seems. Check out Keyshot too if you are interested in an external rendering program. About 2/3 of the price.
-
9 minutes ago, Thor Walter Andersen said:
Thankyou for your replies.
We have a lasercutter in our office. You send files to it like a printer and it reads red lines set to thickness 0.01 as cutting and up to 16 other line colours and thicknesses as engraving with different strength.
I would like to set up everything in Vectorworks and send plot files to it directly without exporting via dwg/dwg and preparing the files in Autocad. (I prefer working i Vectorworks)
Seems like something that should be possible to fix in a later release...
You are obviously not talking about sending an ordinary cutting file to a laser. More like engraving based on colors or shades of gray, which is a completely different thing. This is a different technique also possible do with laser machines but also for milling machines based, but instead of being based on vector couriers, it's based on pictures. What we talked about is actually cutting out contours, which you can also do with a laser. So, two completely different things.
So, perhaps a relevant question is what 0.01 actually means. In VW it refers to millimeters, but I somehow doubt that any normal printer would actually be able to print such a thin line. Probably why the thinnest line is set to 0.05. Perhaps though your number refers to 0.01 inches, which is about 0.254 mm, and so on. Would make so much more sense.
Here is a laser cut I did some years ago on my office laser cutter in acrylic glass. Nice cuts but very smelly.
-
14 hours ago, Thor Walter Andersen said:
Laser cutters are unable to read files prepared from Vectorworks.
If it was possible to set line thickness to 0.01 it would be possible to to prepare the cutting files without exporting to Illustrator or Autocad.
Is this something that could be fixed by a script?Thor Walter Andersen
Just export as an older version DXF. V14 or V12.
The line thickness should be compensated by the the cutter driver if everything works as it should, depending on what material you cut and how thick it is. This applies to closed shapes, where it's obvious if the cut is to be on the inside or outside, or if you have closed shapes inside and already closed shape, for example holes on a given surface. In some variants of DXF, such as then AAMA-DXF (used in the industrial fabrics sector), you have special layer codes for outline cuts, cuts inside an online cut, texts, and just plot lines.
Good idea to limit yourself to lines, arcs, and when using polylines only consisting of line segments and arcs. Avoid anything more complex, such as symbols and groups. Avoid fills of any kind.
Illustrator adds absolutely nothing, as the precision is lower than CAD standard and their DXF converter is crap.
-
Step 2 are as follows:
Import the DXF again into VW. Does it work? Try importing it into another program for reference, for example SolidWorks E-drawings or Dassault Draftsight (Both can be download for free). Does it work ?
If it works, you can be pretty sure that there is something wrong with the CNC side. Check with the supplier. Re-install, and so on.
-
These milling programs often tend to be both a bit flaky and fragile, so here are a few other tips:
- Save as an older version of DXF (try V14 or V12)
- Simplify as much as possible:
- Avoid using symbols
- Avoid using filled objects
- Explode (decompose in VW) objects before exporting and then Undo it back to civilization once exported (many programs have problems with VW polylines consisting of a mixture of corner types, holes etc,
even from bigger suppliers like Adobe, Graphtec Silhouette Studio, etc)
- Check that the receiving program actually reads curves properly. A super safe bet if it's a problem is to use lines, arcs and circles only for 2D paths.
- Export DXF as TEXT and not Binary
- Export and the import it again into VW to see if it reads properly. Test import the model in another free program such as Draftsight or SolidWorks E-drawings (none of them are particularly nice to work with but they do have very competent import filters).
-
-
17 hours ago, Phil hunt said:
Interesting....so what was the final program you used to transfer you model file to key shot.....and was it a steep learning kerb for keyshot. Thanks
The model was direct exported from VW to Keyshot using the Collada format. KeyShot is basically a stand alone rendering program that reads from other programs via plug-ins, but also reads a wide range of file formats. I mostly tested it for product visualization, where it's more easy going than with architectural models.
Rendering quality is by far the best of quite a few programs I used over the years. Very good textures. All materials tested (metallic paint, chrome, rubber, leather, glass ) looks very realistic. The background image used was a stock one, it's 360, and it instantly generates shadows and reflections in the model despite the model not really standing on something, and updates instantly and follows the model when you rotate the model. Photo realistic realtime updates. I'm testing on a demo, so what you see is a screen dump, and it takes say 5-10 seconds to get there after a change of say color of view. Seems to communicate well with VW in all sorts of file formats, including IGES, XT, STEP, DWG, DXF, 3DS, OBJ, VRML, Collada, etc. 3DS and Collada allows you to bring over Renderworks stuff like textures and lights, but where Collada works better as it exports as NURBS models, whereas 3DS exports as trimeshes. So far good then. Bad things, and the this is a colossal flaw, is that it can't smooth off a polygon or trimesh based model (what the ... where they thinking there not being able to do what virtually all other programs can do), and it's also quite expensive.
-
No program does everything, so therefore I almost always use combinations of tools. In this quick sketch, the NURBS surfaces where generated in TouchCAD, the solid modeling was done in VW, and the rendering in Keyshot. With a little practice, I guess it was under a days work, and all programs did something they where good at.
-
1
-
-
13 hours ago, nrkuhl said:
I agree with @Zoomer, the geometry from Sketchup is often revealed to be really terrible when you bring it into other 3D programs. It's often not suitable for any kind of 3D printing without a lot of cleanup.
I have a pretty strong background in Rhino and if I need to do any 3D modeling more complex than a simple box, I usually do it Rhino. VW's modelling is like pulling teeth compared to Rhino. I occasionally 3D print models for work, and I always take the geometry out of VW to clean up in Rhino, because even simple things like joins and subtractions get weird really quickly. VW's NURBS implementation is not particularly useful, extruding can only be done on a limited selection of object types, drawing 3D polylines or curves is difficult, and surface creation is not intuitive either. I'm roughly 300% faster in any program that gives me a command line, vs forcing me to use a limited set of shortcut keys or menu/tool palette selections.
You can also run Rhino on just about anything (seriously, I've run the most recent version on an ARM powered Windows tablet with 1gb of shared video memory). And it's more stable than VW (and cheaper). So if you're looking for a better 3D modeling program than VW, there are definitely options. There's also things like Blender, Solidworks, and all the Autodesk options, the choice of which really depends on what your application is.
I do my architectural drawings in VW because I'm paid to and it's moderately ok at them and cheaper than other BIM options.
It's true that most of us use a combination of programs, depending on what you do and what you wish to achieve. Hands up everyone who uses Photoshop for example. Personally, I have about five or ten programs I consider my core inner circle programs.
I would definitely not use Rhino for the bulk of architectural modeling, and not for 2D drafting. VW's NURBS implementation could be improved a lot (I almost always use another program there and import the geometry, though not Rhino), but just a few clean-ups in the user interface would take it much closer to Rhino, even though Rhino by no means is my favorite, it's still admittedly better than VW at this. Solidworks and the AutoDesk options are way more expensive, and besides Revit, mostly focusing more on mechanical modeling, so they are perhaps in another league. As for Revit and ArchiCAD, I somehow doubt that they are nowhere near as flexible as VW is for things other than Architectural work.
-
Personally, I see no point whatsoever to use SU for anything. Have it installed, but never use it. It looks cute for a few minutes, until you realize that most things takes longer to do than in other programs. The user interface, in my opinion, makes simple things complicated. The VW 2018 program folder is 7.6 times bigger than SU 2017, and the reason is simply that there are much more of everything. Simple can be good if you don't have time to learn a way more complicated program, but also means that you hit the roof of what's possible much quicker. SU has admittedly a far healthier third party market, but much of it is of somewhat questionable quality as it's done by amateurs.
-
4 hours ago, mjm said:
Dang that's good. And how you evaluate Keyshot at this time?
Rendering quality is by far the best of quite a few programs I used over the years. Very good textures. All materials tested (metallic paint, chrome, rubber, leather, glass ) looks very realistic. The background image used was a stock one, it's 360, and it instantly generates shadows and reflections in the model despite the model not really standing on something, and updates instantly and follows the model when you rotate the model. Photo realistic realtime updates. I'm testing on a demo, so what you see are screen dumps from various views, and it takes say 5-10 seconds to get there after a change of say color of view. Seems to communicate well with VW in all sorts of file formats, including IGES, STEP, DWG, DXF, 3DS, OBJ, VRML, Collada, etc. 3DS and Collada allows you to bring over Renderworks stuff like textures and lights, but where Collada works better as it exports as NURBS models whereas 3DS exports as trimeshes. So far good then. Bad things, and the this is a colossal flaw, is that it can't smooth off a polygon or trimesh based model (what the ... where they thinking there not being able to do what virtual all other programs can do), and it's also quite expensive.
-
On 2017-11-08 at 9:29 AM, Claes Lundstrom said:
A much easier way to build for example a fencer is to just generate a clean basic shape, in this case the entire side panel of a car, and then trim out the opening with simple extrusions from the side. In the case a circle with a rectangle extension (add surface) for the wheel arches and a double line polygon for the door gaps.
Just out of personal interest and curiosity, I played around some more with this concept to see if a decent car body shape could actually be extracted using this method. Here is what I did:
I imported five untrimmed surfaces NURBS to start with (top left). I then cut openings for windows, doors, hood, grill, lights, added various panels to fill the openings and some details to make it look a little better in the rendering. I then exported the model to a rendering program called Keyshot (which I'm currently evaluating anyway) for rendering. All in all, I think it took me well under a days work.
-
Had a quick look at your model. Hard to say what the problem is as the main object is a Generic Solid. From the smaller parts though, I noted that it consisted of quite a few more steps than actually required. As a general rule in solid modeling, make a proper plan how to get things done before starting, keep it as simple as possible, do as much as you possibly can in the 2D phase, be very precise during assembly keeping corners exactly edge to edge, avoiding tiny steps, very pointy joints, and leaving fillets and chamfers to the final stages of the process.
-
Corel Draw is probably the best bet for Windows, but it's not available for Mac. AI's support for DXF has always been a bit crappy. For cutting, which I do a lot of, EPS seems to work fine. Affinity is admittedly still in need need of work, but shows promise as a budget option. The same applies to their other Adobe replacement products.
-
I too have a lot of such issues while resisting to spend a not insignificant amount of money on AI, which I would never use for anything other than conversion. My suggestion would be to get Affinity Designer, which costs something like $60 or 70, no subscription fees, reads and writes AI and is a very close competitor to AI in terms of features.
As for CNC export, it explicitly sounds like a cutter like for example a Zund, and there the solution is to use EPS as a first choice and PDF as a second choice, DXF as a third choice, and of course being vector based data only. These files are both directly usable by the two most commonly used programs, AI and Corel Draw. Remember to specify the drawing scale though, as it's exported as the VW paper scale and not in full scale as used in real CAD program formats such as DXF or DWG. The reason for this is that there is no such thing as a drawing scale in these illustration programs.
-
16 hours ago, tringas1 said:
yes, @Claes Lundstrom I'm going for something just like that. I tried "create surface from curves" and it wouldn't read the curve network. Next, I tried the Birail sweep mode from loft surface tool but it likes to make the curve with straight lines as you see above. I'm wondering if it is my graphics card that will not produce the image I want.
Easy enough. I started with a 2D arch, converted it into NURBS, Grouped in and compressed it to get that bumper shape using the scaling handles. I then copied it and made a slightly higher and wider copy and then a second copy of the original. I then moved them apart to that the smaller versions where located on each side of the bigger one. I then lofted the curves into a simple NURBS surface. You can then experiment a bit with the shape bu undoing the lofting and modify the curves a bit until you get the shape you want. Yes it's a plain OpenGL rendering. You could try changing the OpenGL settings to get a better looking result though. The default setting is set to low for rounded shapes and never works properly.
-
Based on my experience in designing similar large real tents, I somehow doubt that subdivision is the way to go. It's simply doesn't give the required shape control, and the movie model doesn't look like a real tent. I think it needs ordinary NURBS modeling where you loft curves.
-
-
19 hours ago, tringas1 said:
I've had to let those surfaces sit a brew for a while, when I come back to them later I'll be able to look at them without frustration.
Here is a detail piece of the car i'm working on i'm trying to smooth the edges out instead of having them in straight section to make up the whole curve.
Using 2 CAD systems
in General Discussion
Posted
No shame in using more than one CAD program. I do it all the time. You can re-paint your house with a screwdriver, but why bother as its' much quicker using a brush.