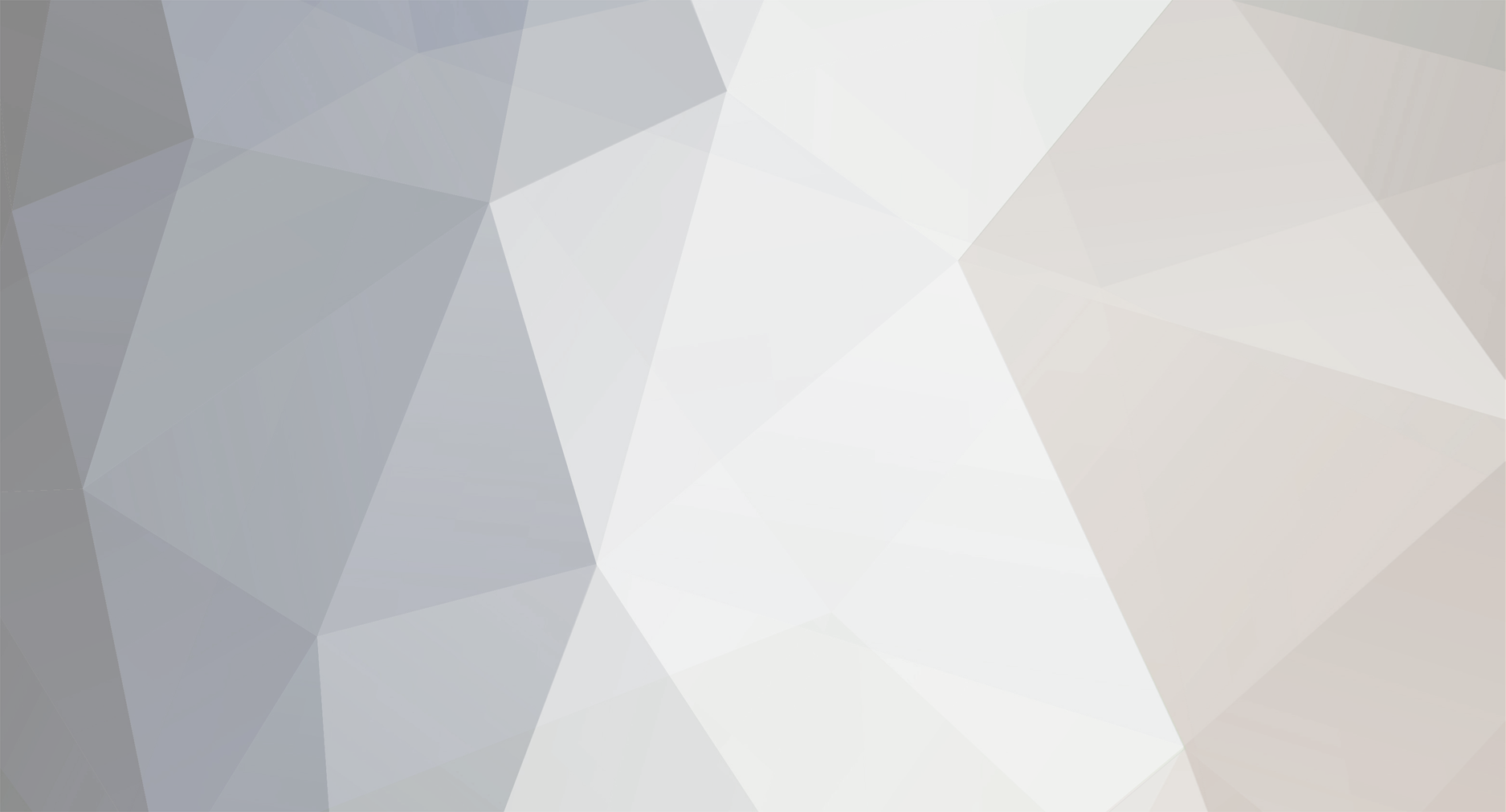
Kevin McAllister
-
Posts
5,162 -
Joined
-
Last visited
Content Type
Profiles
Forums
Events
Articles
Marionette
Store
Posts posted by Kevin McAllister
-
-
Grant,
You can ungroup, just make sure you're in a 3D view. Or duplicate and ungroup twice (once in 3D and once in Top/Plan) if you want both 2D and 3D geometry. It does create some subgroups for some reason however.
Alternate, I copy from within the Auto-Hybrid and then paste outside to get an exact duplicate. Unfortunately, Auto-Hybrid works on its own origin, so likely you will not be able to Paste In Place.
Kevin
-
I agree completely. Convert to Lines and Convert to Polygons have long been in need of an update. Both should understand how to convert curves and more complex objects with holes.
Kevin
-
Yup. It gets more convoluted with every version. My rules are -
- always switch to top/plan view when editing within an extrude. The polygon shape should go from transparent to solid in appearance.
- always draw in screen plane mode when editing.
This usually works. Things that can add to problems include -
- if the extrude is nested in a solid addition, subtraction or section
- if the extrude is nested in a symbol, especially if the instance you are editing is rotated
- if the object has been mirrored.
If all else fails, I copy the polygon object out of the extrude, do the edits and then re-enter the extrude and paste the new object in, deleting the old one.
Good luck.
Kevin
-
The surface array command is actually pretty amazing, all it needs is a good interface designer to bring it into the modern age of software design :-)
Kevin
-
Those solids have a history in VW, so perhaps it has something to do with it? I think it's better if you convert them to a generic solid, so that the history is gone.
I often convert things to generic solids. Sometimes it improves things but mostly the geometry problems remain if they existed, even after conversion. Something that has hairline spaces within it appears as a full solid but isn't really.
Kevin
-
I regularly work in both. I'm still waiting for metric materials - a 4' x 8' sheet of plywood is self explanatory, but 2438mm x 2219mm sheet of plywood doesn't make any sense at all :-)
KM
-
I've been working more and more with Solid Addition, Solid Subtraction, Chamfer, Fillet, Solid Section as my 3D models become more complex. It seems the geometry VW is creating can get messy after a few operations. Often it will be acceptable to work with within Vectorworks, but when exported all of the flaws show. Geometry that should be water tight is not.
Some of the issues I've seen -
- Solid additions retain internal geometry instead of becoming clean solids. This internal geometry shows when exporting as polygon shapes in various export modes.
- Worse still, solids that touch but do not overlap don't actually become a complete solid even though VW thinks they have. They leave holes/gaps which appear when exporting polygon shapes.
- Solid Subtractions flip some of the normals in a subtracted area.
- Solid Subtractions become corrupted, causing bad geometry if any other solids operation is performed on them.
These problems most often appear on export (C4D, STL). However they also cause the re-creation of Auto-Hybrid objects to fail if edits within them cause any of the above conditions.
Its amazing how important good geometry is when sharing between formats or when 3D printing.
Kevin
-
Yes, STL is stereo lithography. I've found that most STL files exported from VW have issues which is why I bring them into C4D for optimization.
If I could export useable STL files directly from VW, you can choose the amount of detail that is exported, geometry wise.
STL problems most often seem to result from Solid Subtractions and Chamfers. Vectorworks seems to flip some of the normals and often leaves holes in geometry when converting.
KM
-
Bruce,
Its possible you could make what you need using the create surface array tool. Its surprisingly powerful.
Kevin
-
I've seen the 2D stair not match the 3D stair quite often. If I remember correctly its specific to one of the stair tools only.
Kevin
-
I've seen the v2013 SP3 bug with dimensions moving in the opposite directions too. Very frustrating. As you say, the fundamental tools need to work and be trusted.
Kevin
-
I would like direct and better control over the resolution of curve geometry sent to Cinema 4D using the Send to Cinema 4D command.
From what I understand, the geometry detail is linked to what is used for Final Quality Renderworks if no render mode is used when the model is sent (ie. model is in wireframe). It can be customized by adjusting the settings for Custom Renderworks and rendering in Custom Renderworks by exporting. This is a non-intuitive, convoluted way of controlling things and even at Very High, curves often don't have enough geometry.
I would like a direct preference and the ability to set a higher conversion resolution than is currently possible.
Kevin
(PS> I am using the VW->C4D->STL workflow for 3D printing which is why more resolution is needed.)
-
Will VW allow you to create a new blank file when it opens? If so, its likely your file that is corrupted, not VW itself.
KM
-
-
I would love the OIP to be able to do more than just step through multiple objects when they are all selected together. It would be great to be able to "deselect all others" when using the step through buttons and finding the object you're interested in.
KM
-
That would be great.
I also wish that the vital info in the OIP (class, layer, plane, name) were fixed when you shifted between the Shape / Data / Render tabs so they were always visible.
KM
-
I agree 100%.
+1
KM
-
I would like better user interface functionality with the Arc Length Dimension Tool. If the tool only allows dimensioning on a single arc, why doesn't clicking on the arc activate the dimension automatically. Its silly to have to select both end points of the arc.
Here's the scenario -
I'm trying to dimension a series of openings along a curved wall. I've drawn a series of arcs that delineate each segment of the wall to be dimensioned. I go to dimension my first arc using the Arc Length Dimension Tool. I select the start point of the first arc and then try selecting the end point. Because the end point of the first arc and the start point of the second arc are coincident the tool fails, giving me the message that I need to select two points on the same arc.
The tool needs to be simpler and smarter than this. Its supposed to make the job easier, not harder and more frustrating.
Enough said,
Kevin
(Yes, yes there are work arounds. Yet more work and less productivity.)
-
1
-
-
You might be able to produce something with the surface array command if you're running VW2013.
KM
-
This is entirely to do with the stacking order being added in VW2013.
As far as I'm concerned the stacking order is only useful in new files and only if multiple sheets can have the same sheet number, otherwise it just gets in the way.
I would like the old dominance to return as the default too. And for VW to re-assign the stacking order to match the sheet number order of the original file when importing from older versions of VW.
One step forward, two steps back....
Kevin
-
Double click on the extrusion. Choose top/plan view and now you should be able to edit the original polygon.
KM
-
Hi Bruce,
If you are asking if you can extrude multiple shapes along the same path, then yes, its easily done. Select all of your shapes and choose Extrude Along Path. The dialog will come up and let you choose which one is the path...
Kevin
-
That's way too forward thinking....
+1
KM
-
Sounds like a "bug" but likely its WAD (working as designed). All these inconsistencies make for a very fragmented workflow....
:-(
Kevin
Auto hybrid, how do I get rid of it?
in General Discussion
Posted
Frustrating isn't it.
My favourite is everything disappearing if you insert a 3D locus into the Auto Hybrid, yet if you insert say a Tube Object, a PIO that contains a 3D locus, it behaves just fine.
KM