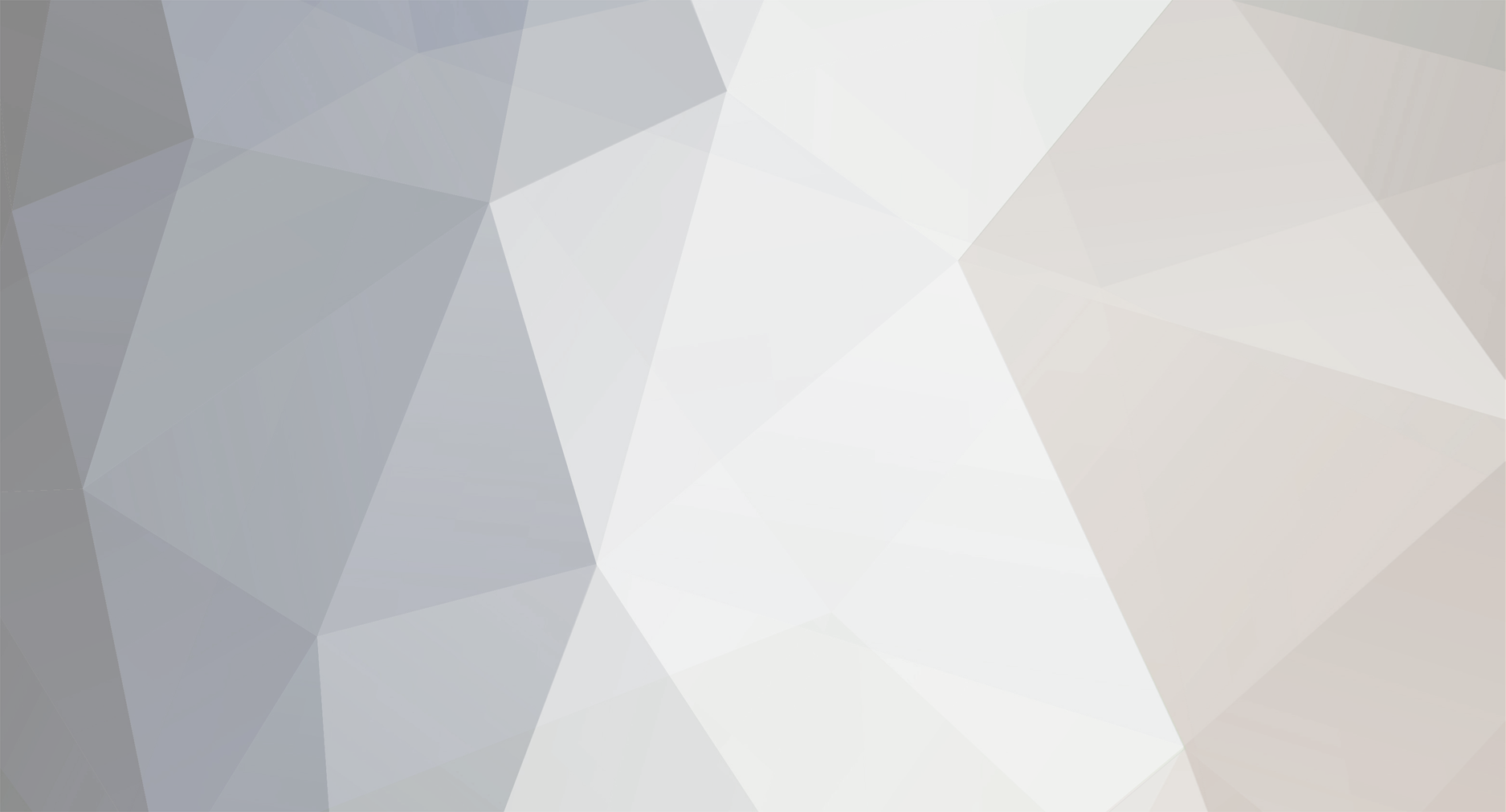
GWS
-
Posts
630 -
Joined
-
Last visited
Content Type
Profiles
Forums
Events
Articles
Marionette
Store
Posts posted by GWS
-
-
I must disagree. They are just 2D dimensions on a layer plane. Wear the layer plane has to be set before applying.
They are not associative
They don't recognise 3D arcs/circles
They don't work in a viewport (2D circles still have to be overlaid)
They don't render properly in a viewport (A second viewport in wireframe has to be overlaid).
-
Bruce I couldn't agree more.
It seems to me that most of the bugs and problems in workflows have come since 2010 and layer/screen planes have screwed up a lot of basic functions.
As far as I am concerned 2009 SP5 was the last good edition.
Objects are often displaced when editing and only reset when cycling through plan view and then back to the current view in use. This is just another 'little' issue that seems to have started since the layer/screen plane implementation, and is a real pain.
...and for all the so-called improvements we still don't have 3D dimensions.
-
I, regretfully, must agree.
I would go so far to say as it has cost me time, productivity and consequently money, not to mention problems with engineering companies and DXF exports.
-
You could use the 3D fillet tool. (Although it has it draw backs)
-
-
-
-
Try changing the fill of the text to none this may help but the quality of the text isn't that great great.
There is a problem with rendering '3D' dimensions in OpenGL especially in viewports, hopefully SP3 will fix this.
When using viewports it is often best to place a viewport directly on top of the rendered one and put the dimensions in that rendered in wireframe, otherwise there are printing issues where the text wont print or export as a PDF.
-
erratic behaviour of the screen/layer plane seems common in 2011. I have no end of trouble with it.
-
Yes Draftsight is very useful and unlike TrueView it runs natively on a Mac
-
No but sounds delightful!
-
You only need to create a DXF file for the view of the profile that you want cut, unless the water jet cutters are actually cutting a 3D object, which I'm not sure is possible.
In other words if you have a plate that is on the XZ or YZ axis, not lying flat on the ground plane, you would need to select either the right or front view so that you would be looking at it square on and then convert to a 2D outline.
Once you have got the outline make sure the view is set to Top/Plan before you export. The converted line or lines shouldn't change their orientation, if they do use the OIP to put them on the screen plane.
-
OK let's say you have one item in one file.
You will probably need to export the file as version 14 DXF or even 12 anything else will cause problems which can range from the water jet not being able to read the file to actually causing a crash....not very helpful.
Make sure, and this is really important, the view is in Top/Plan and nothing else as some CAD/CAM software can read on object on a 3D plane.
The outline or outlines must be single polylines or polygons, so if you modelling in 3D you will need to pick a view of the object and 'convert to lines' to create 2D object but beware as the 2D object can still be on a 3D plane as already mentioned.
Once you have your 2D lines you will have to compose them into one line or polygon.
If you do convert to lines you may want to smooth the curves by going to Modify>Smoothing and then pick an option I usually pick arc smoothing.
This is necessary as VW turns 3D arc or circles into many straight lines causing a faceted finish.
If you have any more specific questions, I'll be happy to try and help.
-
Are you exporting many parts from one file or do the parts have individual files?
-
Hi Nathan,
Make sure that when converting to lines you select 'hidden line rendering' this will help reduce the number of lines.
You will still get many lines on arcs and circles because in the conversion VW converts all curved stuff into many straight lines. How many lines depends on your settings in VW preferences under '2D conversion'.
You can select these lines and compose them into one object but it will still be faceted so you then have to go to Modify>Smoothing and select an option to smooth the composed faceted line. I generally chose the 'arc' option.
I know this is a bit convoluted but I haven't found a better way.
I do a lot of stuff to be sent to laser/water cutting and have to do this a lot.
It would be nice if VW at least convert 3d arcs to 2D arcs in one go!!
-
P.S. It's probably best to tick the box 'Use At Creation', top left on the Class Edit Window, then the newly created object should take on the transparency from the start.
-
You can assign textures to apply to different classes and I usually set-up 2 or 3 textures of varying transparency so each class will render differently.
You can do this through the resource palette by creating a new resource and setting the attributes to 'Object Attribute' and set the transparency to 'Plain'.
In the class edit window go to 'Other textures' and slelect the texture you require.
Once set-up you can edit the different textures in the resource browser quite easily.
-
I think that VW is fundamentally an architectural software package and while it does delve into other areas, Landscape, Spotlight etc it's really focus is architecture.
Machine Design has now been dropped and although there are some parts of it incorporated into the VW Design I doubt it will be developed further.
CAD software is developing quicker and quicker these days and I can't help feeling that VW is just playing catch-up. There are too many basics missing or not working well, one of which is the way VW deals with rendering in OpenGL, namely text on a working plane, faceting of objects, viewport rendering etc.
As far as fluid 3D modelling goes, again there are some basics that are missing, i.e. the inability to alter a fillet easily and in real time makes Product Design hard work and the fact that 'move face' mode in the Push/Pull tool often results in an uneditable Generic Solid.
I have used VW for many years and I have always liked it but if the basics don't get fixed/upgraded I will have to look elsewhere, not something I either want or will enjoy doing.
VW does export STL files which are very useful in Product Design for 3D printing although I have had some difficulties even with that process lately.
So in answer to your question I'm not sure that VW is the best option for Product Design.
-
Hi Rob,
Are you rendering in OpenGL, if so are those settings set to 'very high'.
I often find when adding solids together the surface turns much smoother I think it is because it turns things into NURBS surfaces which are much smoother anyway.
If you convert the object to NURBS what happens then?
-
You can double tap the zoom tool.
Default settings are the 'C' key for zoom in & 'V' key for zoom out. This will zoom in or out by a factor of 2 each time you double tap.
(You can change these keys in the workspace editor)
I don't know how to set it to specific zoom %'s though
-
Perhaps the >alt key could move back one face at a time....it is difficult in a crowded space.
It would also be good if the P/P tool didn't have a tendancy to turn the object into a Generic Solid when using the second option (Move Face) as you then lose all the object history.
-
I have lived with this for so long I seem to have got used to it. I use another CAD program that doesn't have this issue and it is not a high end/high priced piece of software either.
I feel that it just another one to add to the long list of items that don't work properly.
I can only think the reason it is not fixed is because it is too complicated or too deep in the program to be fixed.....otherwise why would you not fix it?
-
I have experienced the same issue.
I find using either zooming in with the mouse wheel or using the snap loupe seems to help.
Sometimes it has snapped to the right place but just doesn't look like it until you have finished the whole dimension.
-
Hi John
I managed to do this by doing a similar process to Kaare's suggestion.
I extracted the 3 lines but before lofting I moved one the points at the tip by a small amount using the OIP.
I then lofted using 2 profiles and a curve (third option) and was then able to shell the surface.
Hope this helps
(I am using VW2011 though)
Screen Plane - Layer Plane
in Wishlist - Feature and Content Requests
Posted
I couldn't agree more